Beyond ROI: Making the Case for Ingredient Automation Investment
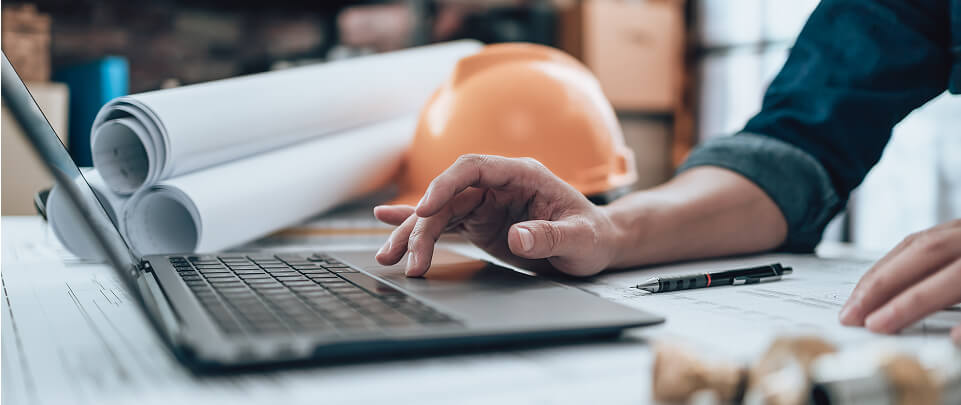
Table of Contents
Step 1 & 2. Assess Current State & Potential Gains
Step 3. Run the Numbers
Step 4. Calculate Value
Start Your ROI Worksheet
Click here to begin building your business case for ROI
Bring ROI Into Focus
When seeking bulk ingredient handling solutions, you might be tempted to hone in on the technical questions first: “What’s the equipment? How much does it cost?”
These are good questions, but not the first ones to ask.
Without a clear understanding of why the project matters and how it will deliver value, it’s easy to miss the mark on return on investment (ROI) — or worse, invest in a solution that doesn’t move the needle. The truth is, it’s not the tech that derails most automation projects — it’s the assumption that ROI will “just happen” without asking the right questions first.
At first, the path to ROI can seem out of focus, like looking through a camera lens that hasn't been adjusted. You see the outlines, but not the opportunities. It's only when you carefully frame the right priorities and bring them into focus that a fuller picture emerges. And in that moment of clarity, you know exactly where to aim for results.
What “results” look like may differ by stakeholder — whether that’s reduced risk, improved compliance, employee retention, or the ability to scale without proportionally increasing costs. In this guide, we help you zoom and sharpen your plan — just like using a camera — to see the value clearly.
Ingredient automation has the potential to unlock serious gains, from labor savings and higher throughput to improved safety and compliance. But those benefits don’t come automatically. They need to be uncovered, measured, and tied back to the broader business case.
We’ve seen it again and again: once company leaders understand where value can be created, they make smarter investment decisions.
After working on thousands of projects with executives, project engineers, plant managers, production VPs, and more, we’ve found that the best automation outcomes happen when leaders are willing to:
- Look at the big picture
- Be open to new ways of thinking
- Tear apart assumptions if needed
- Collaborate to find not just a solution, but the right solution
ROI is realized on a case-by-case basis and it’s different for every organization. So while you might be tasked with solving a single, current technical challenge, we encourage you to take the opportunity to transform your entire plant’s performance.
Redefining ROI: What Value Really Means
At AZO, we define ROI broadly as the tangible and intangible value that automation unlocks. That includes:
- Meeting compliance goals
- Increasing process reliability and quality
- Reducing injury risks and OSHA exposure
- Enhancing employee experience and retention
- Building infrastructure that supports long-term scalability
The Dangers of “I Don’t Know”
One of the most common traps in capital planning is investing weeks in scoping a project, only to discover there’s no business case. That’s a lose-lose for everyone, especially if you’re the one responsible for bringing vendors in.
When it comes to proving the value of an ingredient automation project, here’s our take:
If a project isn’t viable, you should know that early. We’d rather tell you “this won’t work” than waste your time.
Arrive at this understanding by taking a complete inventory of all your unknowns. You know the ones:
- “I don’t know how much downtime this creates.”
- “I don’t know how many people we’d need to scale.”
- “I don’t know what this inefficiency is really costing us.”
That’s what this guide is for: to help you build clarity around the problem, uncover hidden value, and build a case for ingredient automation that earns buy-in at every level of your organization. Let’s get started.
Start With the ‘Why’
25–30%
How much automation can reduce operating costs
BCG
Operational efficiency and cost control are more critical than ever, and automation presents a compelling opportunity to drive significant financial returns.
Research from top consulting firm BCG shows automation can reduce operating costs by as much as 25–30%. But to secure buy-in and make the right business case, you need to go beyond the promise of savings and clearly show the numbers behind the value.
Every successful automation project starts by getting clear on your goals.
Are you trying to streamline existing operations to cut costs?
Or are you looking to scale and grow by increasing output?
Both paths can boost ROI, but they serve different business priorities. If your goal is to capture more market share, for example, expanding your line might generate more value than shaving time off your current processes.
Your “why” will drive every technical decision you make, from the equipment you select to people you partner with to design the automation.
Where Savings Comes From
Automation isn’t just about speed. It delivers value in several ways by:
- Reducing labor costs
- Lowering energy consumption
- Increasing uptime and throughput
- Cutting down on waste and product loss
- Improving compliance and minimizing regulatory risks
These improvements add up fast. That’s why most manufacturers we work with expect to see ROI in just two to three years after implementation. For larger implementations in the multi-millions, expect a five-year ROI.
ROI expectations:
2-3 years for smaller projects, 5 years for larger projects
So, How Do You Actually Quantify Value?
While traditional ROI formulas still matter, they’re just one lens. Strategic automation investments deliver measurable and mission-critical improvements in efficiency, safety, compliance, and throughput.
To quantify the full value of automation, take these steps:
Step 1 & 2. Assess Current State & Potential Gains
After determining the scope of your automation project, it’s time to get clear on what’s not working in your current system so you can associate quantitative dollar values to each.
You might undertake this process with a solutions partner (like us at AZO), whose discovery process connects your issues to real financial impact. For example, maybe that’s:
- An extra $150K/year in labor you didn’t realize you were spending
- Product loss from dust that’s eating into margins
- Inefficient cleaning practices that add downtime and risk cross-contamination
Here are seven main ingredient handling challenges facing manufacturers, as well as the benefits of automation for each. As you work through each section, fill out the questions with an honest assessment of your plant’s current state so you can clearly spot opportunities for ROI.
Ingredient Handling Challenges & Benefits of Automation
1. Labor
Labor is one of the most straightforward — yet most misunderstood — elements of ROI. When evaluating ingredient automation, it’s tempting to focus on headcount reduction alone. But the true cost of labor ROI goes deeper than payroll.
Manual material handling is inherently limited. It may offer flexibility, but it also imposes physical constraints, i.e. you can only add so many people around a machine before you hit diminishing returns. Trying to double output without automation often means running into space, efficiency, or quality bottlenecks. By contrast, automation scales in ways people can’t.
Then there’s the human capital challenge: skilled operators are increasingly difficult to find and retain. The turnover rate in manufacturing continues to rise, and each new hire brings added costs in recruitment, onboarding, and training — not to mention lost productivity during ramp-up.
Over time, as experienced employees leave and newer workers arrive, the average skill level drops, increasing the risk of errors and product inconsistencies. In short, labor inefficiencies don’t just inflate costs — they chip away at system performance, contributing to production loss.
Ingredient automation helps reframe labor. By shifting manual roles into higher-value, skilled positions — like operating, monitoring, and optimizing automated systems — the overall work environment can be enhanced and the workforce upskilled. That translates into better morale, stronger retention, and a system that performs reliably day in and day out.
Labor Challenges
Challenge | How It Affects Value |
---|---|
Manual processes are capped in efficiency | Limits your ability to scale output without exponential labor costs |
Too many people needed to meet demand | Crowding creates safety, coordination, and performance issues |
Skilled labor is hard to find and harder to keep | Leads to frequent retraining, quality dips, and production slowdowns |
High turnover drives up hiring/replacement costs | Impacts cost per unit and operational stability |
Declining skill levels affect quality | Increases waste, rework, and customer dissatisfaction |
Labor Benefits of Ingredient Automation
Benefit | How It Contributes to Value |
---|---|
Reduces dependency on manual labor | Lowers operational costs while boosting consistency |
Enables scalability | Adds capacity without increasing headcount |
Improves quality and repeatability | Fewer errors and waste, better customer satisfaction |
Upskills existing workforce | Increases retention, job satisfaction, and builds internal expertise |
Enhances operator safety and satisfaction | Reduces injuries and absenteeism, improves work environment |
2. Injuries & Death Risks
When calculating ROI, it's easy to overlook safety… until something goes wrong. Workplace injuries don’t just negatively impact people; they disrupt production, trigger investigations, and lead to unplanned costs that ripple throughout an operation.
In facilities handling dry bulk ingredients, injuries often stem from repetitive, physical tasks like lifting heavy bags or manually interacting with equipment. These aren't rare incidents; they're daily risks and the primary source of compensable injuries, according to OSHA. Add combustible dust or slip-and-fall hazards to the mix, and the situation quickly moves from inconvenient to catastrophic.
Beyond the direct human impact, injuries will significantly affect ROI. Lost-time incidents mean lost productivity, plus medical costs, workers' compensation payments, and insurance premium hikes. In the most tragic cases — serious injury or death — the operational, legal, and reputational costs are immeasurable. Use OSHA’s Safety Pays Individual Injury Estimator to assess how occupational injuries and illnesses impact your profitability.
Ingredient automation minimizes exposure to risk by removing people from hazardous tasks. Whether it's reducing manual bag dumping, eliminating the need for operators to enter confined spaces, or implementing dust-tight systems to prevent combustion, automation isn't just about efficiency, but creating a safer, more sustainable workplace.
In some cases, safety alone is the driver. We’ve seen manufacturers greenlight automation projects not because of the bottom line, but because they removed unacceptable risks.
Injuries & Death Risks Challenges
Challenge | How It Affects Value |
---|---|
Manual lifting, repetitive motion, and fatigue | Leads to ergonomic injuries, lost-time incidents, and increased workers’ comp claims |
Exposure to dust, allergens, or chemicals | Triggers health concerns and compliance issues |
Risk of combustible dust | Raises potential for fires or explosions, increasing liability and insurance costs |
Lack of guarding or automation around hazardous processes | Increases the chance of critical injury or OSHA violations |
Inconsistent safety practices or training | Causes variability and elevates risk exposure plant-wide |
Injuries & Death Risks Benefits of Ingredient Automation
Challenge | How It Affects Value |
---|---|
Reduces physical strain and injury risk | Lowers absenteeism, turnover, and compensation claims |
Minimizes exposure to dangerous materials | Enhances regulatory compliance and operator health |
Decreases risk of explosion or fire | Protects people, product, and plant from catastrophic events |
Enables better safety standardization | Builds long-term safety culture and process control |
Helps meet OSHA and NFPA compliance | Avoids costly citations and keeps operations running smoothly |
3. Material Sourcing
As production needs evolve, so do sourcing strategies. Many manufacturers start with exploring ways to receive ingredients in larger quantities — such as super sacks or bulk truckloads — to reduce delivery frequency and the time it takes to unload materials. These changes streamline material handling and tend to unlock opportunities for volume-based pricing and more efficient supply chain planning.
By increasing container sizes or optimizing transfer methods, you can move materials more efficiently through the system. For example, where an operator might unload 50 pound bags for 20 minutes to hit a production target, that same operator can unload a super sack containing the same volume in just half the time — and often run multiple stations simultaneously. It would take five or more people to match that automation speed.
It’s important to note that automating and scaling the material sourcing process isn’t about doing away with the systems that work. It’s about building on them — creating a more agile, efficient setup that supports future growth while reducing operational strain in the present.
Material Sourcing Challenges
Challenge | How It Affects Value |
---|---|
Smaller packaging formats require more handling | Increases labor time and slows down throughput |
Limited storage or delivery options | Adds complexity to scheduling and inventory management |
Manual unloading can be time-consuming | Reduces availability of skilled labor for other tasks |
Varying ingredient flow rates | May create bottlenecks or inconsistencies in production |
Supplier limitations or delivery frequency | Can constrain scale or drive up per-unit costs |
Material Sourcing Benefits of Ingredient Automation
Benefit | How It Contributes to Value |
---|---|
Supports bulk formats like super sacks or trucks | Reduces labor requirements and increases unloading speed |
Streamlines material flow into production | Improves batch timing, blending consistency, and output |
Enables larger volume purchases | Offers potential savings through supplier pricing or fewer deliveries |
Frees up skilled labor for higher-value tasks | Increases plant flexibility and responsiveness |
Builds a foundation for future scale | Makes it easier to expand lines or add new products over time |
4. Safety & Ergonomics
Shaving 3.2 seconds from a task can reduce direct labor costs by
$ 29,000 a year.
American Society of Safety Professionals
Not every project is driven by dollars alone. For ingredient handling, safety is often the leading reason companies pursue automation — even when the ROI on paper doesn’t seem strong.
That’s because operator safety and plant safety aren’t optional. But there’s another side to the safety story: ergonomics can enhance productivity. This happens in two ways: one, by eliminating non-value-added tasks, and secondly, reducing motion waste. Improvements that reduce physical strain or streamline a manual task protect people and result in measurable gains.
According to the American Society of Safety Professionals (ASSP), even shaving just 3.2 seconds from a task can save up to $29,000 per year in direct labor costs. Small changes, when repeated hundreds of times per shift, add up fast.
Automation helps eliminate the most physically taxing and hazardous tasks. By reducing strain and improving workstation design, employees work more comfortably and consistently — and operations run more smoothly as a result. Safety doesn’t just protect ROI; in many cases, it creates it.
Safety & Ergonomics Challenges
Challenge | How It Affects Value |
---|---|
Repetitive manual tasks | Increased risk of injury and operator fatigue |
Heavy lifting requirements | Potential for acute injury and long-term health issues |
Dust exposure during material handling | Respiratory hazards and potential product contamination |
Inadequate equipment design | Operator discomfort and decreased productivity |
High injury-related absenteeism | Disruptions in workflow and increased labor costs |
Safety & Ergonomics Benefits of Ingredient Automation
Benefit | How It Contributes to Value |
---|---|
Reduced risk of workplace injuries | Lower medical and compensation costs; improved employee retention |
Enhanced operator comfort | Increased productivity and job satisfaction |
Improved dust containment | Healthier work environment and compliance with safety regulations |
Streamlined material handling processes | Decreased downtime and consistent product quality |
Positive workplace culture | Attraction and retention of skilled workforce |
5. Compliance
Compliance in bulk ingredient handling is a critical component of risk management and brand protection. No matter your industry — food, pharma, chemical, plastics, and more — meeting safety and environmental regulations is non-negotiable.
For many companies, compliance requirements are the very reason an automation project gets greenlit, even if it’s difficult to quantify the return on investment upfront. Regulatory compliance includes collecting dust, reducing cross-contamination risks, and eliminating combustible dust hazards. Essentially, automation is a proactive step toward protecting your people and your business.
Organizations like the National Fire Protection Association (NFPA), OSH), and the FDA set standards and rules with varying degrees of complexity. These standards also change over time: for example, the NFPA 660 standard released in 2024 consolidates multiple dust-related guidelines, streamlining dust hazard analysis (DHA) requirements across industries.
Improving automation in ingredient handling helps you pass inspections, but more importantly it can prevent allergen insertion or dust accumulation, increase uptime, and boost product quality. Compliance is a driver for better processes, and that’s where hidden ROI tends to live.
Compliance Challenges
Challenge | How It Affects Value |
---|---|
Dust accumulation or uncontrolled emissions | Raises risk of explosion, citations, and shutdowns |
Lack of traceability in material flow | Makes audits more difficult and limits process transparency |
Manual handling of allergenic or hazardous materials | Increases cross-contamination risk and complicates sanitation |
Evolving regulatory requirements | Creates the potential for costly retrofits |
Reactive vs. proactive approach to compliance | Leads to last-minute fixes instead of long-term solutions |
Compliance Benefits of Ingredient Automation
Benefit | How It Contributes to Value |
---|---|
Helps meet OSHA, NFPA, and FDA standards | Reduces risk of fines, citations, or shutdowns |
Supports dust hazard analysis (DHA) and combustible dust controls | Enhances plant safety and system design |
Improves containment and segregation of allergens | Reduces risk of recalls and cross-contamination |
Enables better process traceability and documentation | Simplifies audits and improves quality assurance |
Positive workplace culture | Attraction and retention of skilled workforce |
6. Cleaning & Maintenance
Cleaning and maintenance often fly under the radar during early project planning, but ignoring these factors can be a costly mistake. Poor dust management, hard-to-clean designs, and frequent maintenance shutdowns can eat into uptime, drive up labor costs, and open up possible exposure to compliance risks and litigation.
What if you could take your system from 79% efficiency to exceeding 100% capacity? Through proactive system improvements, including real-time performance analytics and predictive maintenance, we helped a manufacturer do just that. They saw improved production speed and reduced waste, demonstrating the significant ROI achievable through ingredient automation.
And as we’ve seen with other manufacturers, making a shift from open systems to enclosed, automated ones is a game-changer. Contamination issues are prevalent in nearly all industries. Eliminate ingredient contamination risks by replacing an open belt conveyor with a closed, pneumatic conveying system. Not only does this upgrade safeguard product quality, but it can dramatically reduce cleaning labor and unplanned downtime.
The takeaway: When systems stay cleaner and are easier to maintain, the bottom line benefits. Just make sure there are also housekeeping practices in place.
Cleaning & Maintenance Challenges
Challenge | How It Affects Value |
---|---|
Open conveying systems or manual transfers | Increase dust accumulation, contamination risks, and sanitation labor |
Frequent maintenance shutdowns | Lower overall system uptime and throughput |
Hard-to-access equipment for cleaning | Adds labor time, slows changeovers, and risks incomplete sanitation |
Dust buildup in critical areas | Raises explosion risk and compliance concerns |
Manual cleaning procedures | Increases variability, human error, and operational inefficiency |
Cleaning & Maintenance Benefits of Ingredient Automation
Benefit | How It Contributes to Value |
---|---|
Enclosed, dust-tight systems | Reduce contamination, dust collection needs, and manual cleaning labor |
Easier access for cleaning and inspection | Speeds up sanitation and changeovers, increasing uptime |
Automated clean-in-place (CIP) options | Minimize manual intervention and downtime |
Reduced maintenance frequency | Lowers labor and parts costs over time |
Improved housekeeping | Enhances safety, compliance, and overall plant image |
7. System Performance
Even the best-designed system won’t deliver ROI if it doesn’t perform consistently. Dust issues, bottlenecks, inefficient material flow, and improperly sized equipment can all degrade system performance over time, leading to hidden operational losses.
If a system can’t operate at its intended efficiency, you won’t see the fullest possible return on your investment — and you might be incurring extra costs just to keep production moving.
Manufacturing.net reports that product waste from bottlenecks alone costs the global economy $12 trillion in losses. And at least 25 percent of those bottlenecks could be avoided through efficient and better process design.
Ingredient automation projects should aim to solve immediate pain points and to optimize flow, reduce manual intervention, and maximize output. When every part of your process is aligned and operating as designed, you see the real gains: higher yields, lower energy costs, fewer disruptions, and better quality. For example, just by addressing bottlenecks, you can improve productivity by 15-18%, reports the Amrita School of Engineering.
25% of all manufacturing bottlenecks
are caused by inefficient or incapable process design.
Department of Mechanical Engineering, Covenant University
System Performance Challenges
Challenge | How It Affects Value |
---|---|
Dust and buildup in lines or filters | Cause flow restrictions, clogs, and increased downtime |
Poorly integrated components | Create bottlenecks and inefficiencies between process stages |
Inconsistent material feed rates | Affect product quality and production speeds |
Over- or under-sized equipment | Increases wear, energy usage, and maintenance needs |
Lack of system visibility and control | Makes it harder to optimize performance and prevent issues proactively |
System Performance Benefits of Ingredient Automation
Benefit | How It Contributes to Value |
---|---|
Optimized material flow | Improves consistency, quality, and throughput |
Correctly sized and integrated equipment | Maximizes system uptime and efficiency |
Reduced system backups and clogs | Decreases unplanned downtime and labor costs |
Real-time monitoring and control | Enables proactive maintenance and performance tuning |
Better energy efficiency | Reduces operational costs and environmental footprint |
Step 3. Run the Numbers
“What’s this going to save — and what’s it going to cost?”
Now that we've defined current challenges and the potential benefits of ingredient automation, it’s time to translate each into numbers. If you aren’t sure about the specific cost associated with an issue, here’s a rough estimate for many common scenarios:
Category | Details & Assumptions | Value |
---|---|---|
Labor savings |
|
$165,000 |
Material Format Savings |
|
$150,000 |
Product Loss Savings |
|
|
Total Annual Savings | Labor + Material format + Product loss | $340,000 |
Investment (Cost of Solution) | ROM cost for AZO’s proposed solution | $800,000 |
ROI Period | Investment ÷ Annual Savings | 2.35 years (~28 months) |
These add up to an annual savings estimate that you can compare to your initial investment cost (which you’ll calculate next) to see if the overall project nets a positive ROI.
Note: Not all ROI is immediate. Some improvements (like better safety or quality) lead to savings over time — especially when they prevent future costs or recalls. For multi-million dollar projects, it may take five years to realize ROI. For smaller projects, two to three years is reasonable.
Initial Investment Cost
Now, add up your total upfront investment estimate. This may include:
- Training
- Financing costs
- Equipment costs
- Installation costs
- Facility modifications
- Ongoing maintenance costs
Step 4. Calculate Value
After defining challenges and estimating both costs and benefits, it’s time to frame the investment in terms that matter to decision makers. This means using one or more financial metrics that demonstrate not only if the project pays off, but how and when.
There’s no one-size-fits-all formula. Some stakeholders want to see short-term payback. Others care about long-term internal rate of return. Use an approach — or combination of approaches — that aligns with your audience and business goals.
Not sure which metric to choose?
ROI shows impact. IRR shows efficiency. NPV shows total value. Payback Period shows timing. Together, they offer clarity on the best path forward.
ROI (Return on Investment)
Best for:
Simple, quick snapshot of profitability
ROI = (Annual Savings ÷ Investment Cost) × 100
Example:
If your project saves $500,000 per year and costs $1,250,000
ROI = (500,000 ÷ 1,250,000) × 100 = 40%
This is often the first number executives want to see. But remember, ROI doesn’t account for time. That’s where IRR and Payback Period come in.
Payback Period
Best for:
Showing how quickly the investment recoups its cost
Payback Period = Investment Cost ÷ Annual Savings
Example:
$1,250,000 ÷ $500,000 = 2.5 years
This is a straightforward way to set expectations. A shorter payback period (2-3 years) is generally seen as lower risk, while a longer one (5 years) may be acceptable for larger, strategic investments.
NPV (Net Present Value)
Best for:
Showing how quickly the investment recoups its cost
NPV = Total Present Value of Benefits – Total Present Value of Costs
NPV puts all future cash flows (savings or revenue) into today’s dollars, using a discount rate to account for risk and inflation. A positive NPV means your project adds value; negative NPV means it doesn’t.
This metric is especially useful for longer-term or multi-phase projects where benefits accrue over 5+ years.
Let’s Talk Automation
Making the case for automation isn’t just about crunching numbers — it’s about clearly framing the value your project brings to the business. When challenges are connected to outcomes and outcomes to priorities, the path forward becomes clear.
Whether you're navigating labor shortages, compliance risks, or production inefficiencies, the right solution starts with the right conversation.
Talk to AZO about your ingredient handling goals. We’ll help you uncover hidden value — and build a solution that fits.