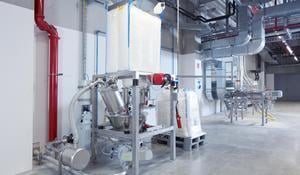
When manufacturers think about optimizing their production line, filtration is rarely the first thing that comes to mind. But whether you're handling food, plastics, or chemical ingredients, the role of industrial filtration systems in production performance can’t be ignored
From improving system throughput to meeting NFPA standards and preserving employee safety, the right filtration system is more than a maintenance item. It’s a profit driver.
Let’s break down how filtration impacts your system’s performance, sustainability, and long-term costs, so you can see why maintaining, upgrading, or right-sizing your filters pays off.
Why Industrial Filtration Matters in Manufacturing
Filtration is the quiet workhorse of bulk material handling. It ensures that air and material are separated cleanly during transfer, and that dust collection is effectively contained. If not properly mitigated, dust is a significant safety hazard for industrial processes.
Updated NFPA 660 standards include stricter requirements for small-volume dust collectors and separators, making it important to have proper filter selection, pressure differential monitoring, and containment design.
But filtration’s role extends even beyond air pollution in the work environment. Poor or inefficient filtration affects your operations negatively in many ways:
- Reduced conveying performance due to pressure imbalances
- Clogged filters that slow or stall material transfer
- Excessive energy use from overworked blowers and motors
- Unsafe working conditions from dust particles
- Non-compliance risks tied to combustible dust hazards
- Unplanned downtime and costly maintenance
These issues may start small and even be minor at first. But filters that require frequent changeouts or allow pressure drop to go unmonitored can create ripple effects throughout a production line, increasing energy consumption and operational wear. Think slower fills and higher amperage on motors. Over time, these side effects can drain productivity which impacts your bottom line.
Achieving Efficiency With Industrial Filtration and Airflow
For filtration in industrial applications, efficiency is about more than a HEPA rating and clean air — it’s ensuring consistent system performance.
Filters protect equipment by working in tandem with airflow systems. Poorly maintained or clogged filters can extend convey times, driving up energy consumption and increasing the risk of uncontained, hazardous dust in the environment. Easy access to filter maintenance is essential so your pneumatic conveying system can work optimally with minimal downtime.
A well-balanced system, fine-tuned for the correct airflow and regularly maintained, operates more efficiently and sustainably. Lower air requirements and smarter power usage translate directly into reduced operating costs and a longer system lifespan.
Filtration Case Study
Consider a dry mix manufacturer we worked with on food processing. Their system experienced motor strain and dangerous dust buildup when maltodextrin — an aerated, floodable ingredient — was swapped for sugar. Because of the different ingredient flow properties, the filter fan had to be shut off, creating a dust hazard and explosion risk.
To resolve this issue, we redesigned the filter placement and added a pressure differential indicator to monitor filter performance, among other changes. As a result, the filtration system operates without quality issues, and dust and explosion hazards have been resolved.
Industrial Filtration Built for Sustainability
Sustainability in manufacturing goes beyond material choices — it’s built into the systems that keep production running cleanly and efficiently. Filtration is one of those systems, and the filters you choose — and how often they’re replaced — depend on the ingredients you’re handling.
Fine particulates such as powdered sugar, fumed silica, and resin that heats and creates angel hair can easily clog filters. For pneumatic vacuum systems to operate well, take inventory of all your filters and create a spare parts inventory so filters can be changed well before a breakdown happens.
If you’re handling hazardous substances, including carcinogenic raw materials, you’ll need advanced filtration like that found in our Toxi-Container, which focuses on removing contaminants by replacing the entire air volume approximately 14 times per hour.
Another filtration system option is secondary dust filters, an essential component in vacuum conveying systems across the food, plastics, and chemical industries. Instead of just collecting dust, our dust filters support cleaner operations by using less energy, lasting longer, and requiring fewer interventions. These dust filters even clean themselves automatically!
Filter Performance Begins With the Right Setup
Focusing solely on filter type is like seeing the forest for the trees — you have to consider your ingredients and the setup to know whether filtration systems are effective. We’re proactive in partnering with you to design your system for optimal filtration. Here are two main challenges:
-
Not all dust behaves the same. That’s why AZO conducts in-house lab testing to evaluate factors like flowability and floodability so each system works for the material it handles. This proactive testing helps avoid oversizing, clogs, and hazardous pressure buildup.
-
Filters that are hard to reach or clean add unnecessary hours to maintenance cycles. That’s why AZO’s systems prioritize accessibility, making it easier to monitor pressure drop, remove accumulated dust, and replace filter elements. This cuts downtime, extends equipment life, and improves overall system throughput.
In manufacturing environments that manage fine or combustible dust, smart industrial filtration makes the environment cleaner, safer, and more cost-effective to operate. With lower maintenance demands, more stable airflow, and fewer equipment failures, filtration becomes a practical path toward meeting sustainability goals while protecting both people and the bottom line.
Need to upgrade your filtration system or replace your filters? Contact us today.