Bulk Ingredient Discharging
Introduction
Bulk discharging of large quantities of solid ingredients or materials is a common process in nearly every industry. No matter what the material might be, efficient operations require large volumes of raw ingredients to be unloaded, moved, or transferred for further processing or production.
When properly designed and engineered, a bulk ingredient discharging solution streamlines these operations, saving time and reducing costs. Systems utilizing custom designed equipment — such as conveyors or bins — enable operators to quickly and safely unload ingredients in a controlled manner, minimizing the risk of contamination or slowed production. By facilitating smooth material flow, a bulk ingredient handling system allows a manufacturer to meet production demands while maintaining a high level of product quality.
Bulk ingredient discharging can present several challenges that could significantly impact operations if the system is not properly designed. One of the primary challenges is achieving efficient and timely transfer of bulk ingredients from delivery to storage to production. This process can be hindered by clogs or blockages anywhere in the system, resulting in delays and disrupting the production schedule.
Another challenge is ensuring accurate measurement of the discharged bulk ingredients. Material that is not free flowing will be difficult to weigh, resulting in quantity or quality discrepancies. These discrepancies can cause to out-of-spec batches which can lead to issues in the final product. The results? Inconsistent quality, unhappy customers, or even product recalls. These issues can occur any time ingredients are stored in silos, bins, or even in conveying lines.
Benefits of Efficient Bulk Ingredient Discharging
Improved Handling and Processing
Bulk ingredient discharging designs can significantly impact the time and effort required for unloading large quantities of materials — the very definition of productivity. A well-designed system will eliminate unnecessary delays and bottlenecks, ensuring a streamlined process with continuous and reliable ingredient flow.
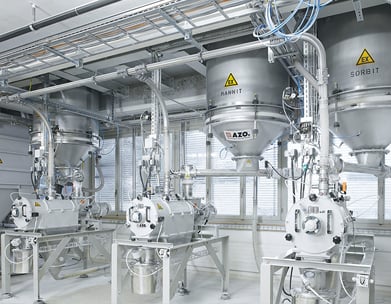
Reduction of Waste and Product Loss
Reliable bulk ingredient discharging ensures accurate weighments, minimizing the risk of recipe variance or bad product. This enhances the quality and safety of the final product while reducing production costs.
Improved Work Conditions
Efficient bulk ingredient discharging supports safer work environments, eliminates repetitive injury risks, and reduces direct labor costs. It minimizes downtime caused by either plugged lines or slow-moving product, thereby maximizing production utilization. These systems should also be designed with a focus on ergonomics, which will reduce operators’ risk of repetitive motion injuries and freeing them to handle more value-added tasks.
Better Space Utilization
Because bulk ingredient discharging systems enable quick unloading and more organized material storage processes, they help optimize storage space. Good design and engineering expertise is especially critical in greenfield designs to ensure the new plant achieves the required production capacity. This improves operational efficiency and reduces costs, enhancing the overall productivity and profitability of businesses.
Factors to Consider when Choosing Bulk Ingredient Discharging Solutions
Type and Nature of the Bulk Ingredients
Different materials may have distinct characteristics that require unique bulk ingredient discharging methods. For example, some ingredients may be prone to clumping or tend to create an excessive amount of dust. These materials require different discharging solutions that can prevent or manage these issues. Understanding the properties of each bulk ingredient is crucial in selecting the optimal discharging solution to avoid any potential or future problems or inefficiencies.
Required Discharge Rate or Capacity
The volume of bulk ingredients that need to be discharged within a specific time frame is another design requirement that will determine the size and capacity of the discharging solution. It is essential to design a system that can handle the necessary discharge rate of each material used within a manufacturing process to prevent bottlenecks or delays. In this case, the chain is only as strong as its weakest link.
Available Space and Layout of the Facility
Production system layout and available space should be considered when evaluating potential any bulk material discharger. This ensures that the chosen discharging solution can be easily installed and maintained. This is especially important when integrating new discharge equipment into an existing manufacturing plant.
Compatibility of the Discharging Solution with System
The optimal bulk bag discharging solution should seamlessly fit into the existing workflow and integrate with other equipment and systems. It is important to evaluate the compatibility of the discharging solution with existing equipment — such as conveyors, mixers, or packaging systems — to ensure actual performance meets design expectations.
Ease of Maintenance, Reliability, and Safety Features
Regular maintenance and easy access to the bulk bag discharging unit’s critical components minimizes downtime and ensures consistent performance. Safety features — such as dust control mechanisms or explosion prevention systems — may also be necessary depending on the nature of the bulk ingredients being handled or required by local government regulation.
Questions About Bulk Ingredient Discharging?
AZO’s Solutions for Bulk Ingredient Discharging
Bulk Bag Unloaders
AZO’s Bulk Bag Unloaders safely and efficiently empty bulk bags containing a wide variety of ingredients. They often feature integrated bag massagers, dust control equipment, and safety features to protect workers. Versatile and customizable to match the unique handling properties of a wide range of ingredients, AZO Bulk Bag Unloaders are a popular choice for many applications.
Pneumatic Conveying Systems
AZO’s Pneumatic Conveying Systems utilize vacuum pressure to transport ingredients from delivery points to storage vessels to processing equipment. Vacuum pneumatic conveying is particularly suitable for handling powders or granular materials and offers superior dust control. It also offers flow flexibility in terms of distance, volume, and direction, making it ideal for large-scale operations. Pneumatic conveying systems should be customized to meet the specific requirements of each ingredient.
Bulk Bag Dumps
AZO’s Bulk Bag Dumps safely and effectively empty bulk bags of various sizes (25- to 100-pounds) which are used for materials, including powders, granules, and flakes. Designed specifically for manual unloading, they feature sturdy construction and advanced features. This equipment ensures smooth, seamless flow of ingredients from the bags into downstream processes while safeguarding operators.
Additionally, AZO can customize its Bulk Bag Dumps to meet specific requirements. Customization options include adjustable height, dust control systems, and different discharge methods from the bottom of the storage bin. This makes AZO’s Bulk Bag Dumps versatile and suitable for a wide range of industries, including food processing, pharmaceuticals, and chemicals.
Bulk Container Dischargers
AZO’s Bulk Container Dischargers efficiently empty any container, such as bins, drums, or silos used to store various types of bulk materials. These dischargers are installed in the bottoms of these vessels and are specifically designed to match the flow rate, material specifications, and weighment requirements. They play a crucial role in industries like food processing, pharmaceuticals, and chemicals, where the accurate and reliable movement and transfer of bulk ingredients are necessary to meet production challenges.
Equipped with advanced technologies and features that ensure smooth, controlled material transfer, AZO’s Bulk Container Dischargers minimize waste and maximize productivity. They can be designed to handle a wide range of bulk ingredients — including powders, granules, and mixes — making them versatile and adaptable to different manufacturing processes.
Trust AZO for Your Bulk Ingredient Discharging Needs
Efficient bulk ingredient discharging plays a crucial role in just about any industry that uses bulk powdered material in its production process. AZO’s discharging systems offer benefits that contribute to increased productivity and cost savings.
Designed for maximum efficiency, AZO’s bulk ingredient discharging equipment ensures faster and more accurate material transfer. This reduces downtime and enhances overall production efficiency. Additionally, efficient bulk ingredient discharging allows for better inventory management and cost control by optimizing material usage and reducing excess inventory.
By investing in a bulk ingredient discharging system from AZO, manufacturers can streamline their discharging process, enhance operational efficiency, improve customer satisfaction, and remain competitive in today's fast-paced business environment.
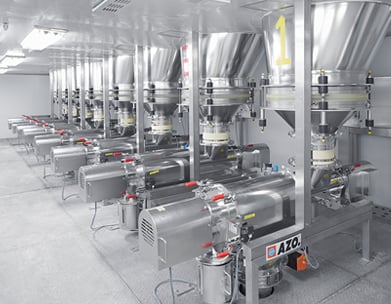
Resources About Automated Ingredient Delumping/Crushing
Solutions
Pneumatic Conveying
Pneumatic Conveying Systems by AZO provide an ideal way for manufacturers to link stages in the process without any risk of damaging sensitive products.
Solutions
Buying A Bulk Bag Unloader
An engineers & executives guide to specifying, justifying, buying and deploying the right bulk discharge solution.
Solutions
Modular Discharge Station
This modular system allows for custom configuration to meet individual requirements for discharging bulk materials.