AZO’s precision batching systems are tailored specifically to meet different material, accuracy, and operational needs. AZO’s various weighing systems employ different techniques to meet both technical and budget requirements.
Bulk Ingredient Handling in the Mixes and Blends Industry
Create the precise, repeatable, and consistent food and beverage blends and mixes consumers expect with an engineered dry bulk ingredient handling system that’s reliable, safe, and productive.
Bulk Ingredient Handling for the Mixes and Blends Industry: Overview
Whether it's dry mixes for homemade baked goods or powdered blends for seasoning a meal or flavoring water, the vast range of bulk ingredients used to create mixes and blends — such as sugar, bits, morsels, and inclusions, or milk powder — is just one of many challenges faced in the industry. Beyond managing the variety of unique ingredient characteristics, bulk handling systems must also provide dependable first-in/first-out flow to maximize product freshness, maintain batch control, preserve product purity, and mitigate dust. Whether a recipe calls for powders, grains, granules, micro ingredients, or add-ins, AZO’s engineering team will deliver the optimal bulk ingredient handling solution that combines safety, accuracy, and reliability.
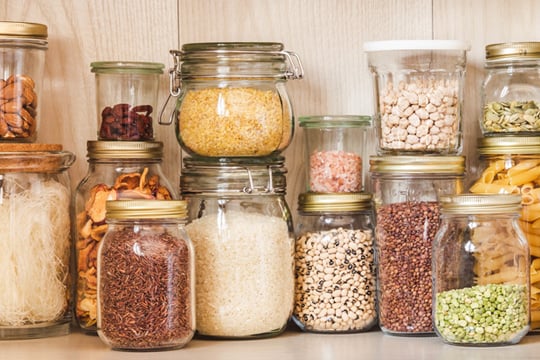
Typical Mixes & Blends Industry System
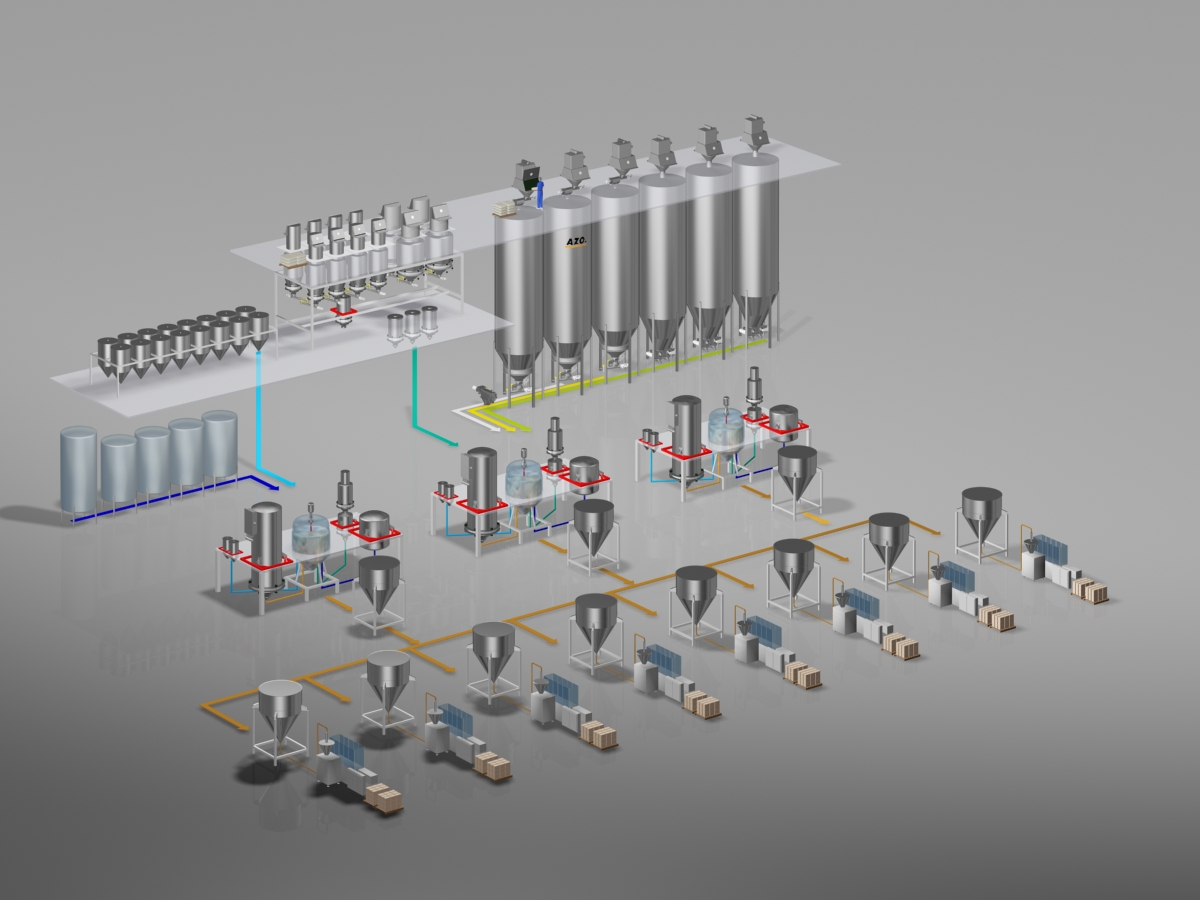
Liquid Ingredient Storage
For liquid and viscous materials, AZO offers tanks in various shapes and sizes, each equipped with features to ensure exacting storage and controlled processing.
Bulk Ingredient Scale Receiver
AZO’s precision batching systems are tailored specifically to meet different material, accuracy, and operational needs. AZO’s various weighing systems employ different techniques to meet both technical and budget requirements.
Minor Ingredient Scale Receiver
Linear Componenter
COMPONENTER® batching equipment from AZO offers a highly accurate, automated dosing and weighing system for minor and micro-ingredients.
Ingredient Feeding Station
Raw Ingredient Storage Silo
Robust and space-efficient, AZO’s silos provide vertical storage solutions for dry and free-flowing bulk ingredients.
Major Ingredient Scale Receiver
Batch Container
COMPONENTER® batching equipment from AZO offers a highly accurate, automated dosing and weighing system for minor and micro-ingredients.
Packaging Machine (Equipment by Customer)
Bulk Ingredient Handling for the Mixes and Blends Industry: Common Challenges

Mix and blend manufacturers must meet hygiene and consumer safety requirements.

Mix and blend manufacturers must meet hygiene and consumer safety requirements.
Food safety is a critical concern for mix and blend manufacturers, as contamination can not only affect end product quality, but also pose risks to consumers. Whether dosing or weighing, mix and blend manufacturers must comply with proper hygienic handling practices for all bulk ingredients through regular sanitation and wash-downs. They must also eliminate cross-contamination risks, verify cleanliness, and prevent ingredient cross-contact.

Variety of bulk mix and blend ingredient characteristics.

Variety of bulk mix and blend ingredient characteristics.
There is an enormous variety of ingredients used in mix and blend manufacturing. The form and characteristics of each ingredient must be considered during the design and engineering of the bulk handling system to ensure accurate dosing and continuous flow. Good engineering in design prevents unexpected surprises during start-up.

Preservation of blend integrity from mixing to packaging.

Preservation of blend integrity from mixing to packaging.
Mixes and blends that incorporate bits, morsels, or inclusions must be carefully conveyed from the mixer to packaging so as to prevent the add-ins from damage during transfer. Further, this process must ensure blend integrity is maintained, avoiding separation and stratification.

New ingredients and changing mix and blend recipes.

New ingredients and changing mix and blend recipes.
To keep pace with constantly evolving trends and consumer preferences, mix and blend recipes can often change, with new ingredients introduced and other ingredients eliminated. These new bulk ingredients can present new handling challenges in an existing system, requiring process or equipment adjustments.

Mix and blend manufacturers must contain dust.

Mix and blend manufacturers must contain dust.
A method for containing the high volumes of dust generated by many bulk ingredients used in mix and blend manufacturing should be included in every bulk material handling system design. Fugitive dust can lead to any number of problems, including attracting vermin, operator exposure, or in the worst case, combustion. Improper dust control creates an unsafe working environment for personnel and increases the risk of product contamination.

Bulk ingredient handling requires space for explosion protection.

Bulk ingredient handling requires space for explosion protection.
Bulk ingredient handling systems must include appropriate explosion protection and dust mitigation equipment. This is especially important when upgrading legacy systems, which may require some design creativity to ensure that necessary protection can fit into the available space.

Government regulation and accurate lot tracking.

Government regulation and accurate lot tracking.
Government requirements for safe food handling and manufacturing include mandates for accurate tracking of every bulk ingredient used in each batch of mixes or blends. Compliance failures such as inaccurate batching or documentation errors — mistakes that commonly occur in manual handling applications — significantly increase the risk of fines or quality issues.

Proper storage and isolation of bulk ingredients.

Proper storage and isolation of bulk ingredients.
Individually storing and isolating bulk ingredients from one another is a critical challenge. Many mixing and blending facilities must handle different ingredients with different characteristics and in significantly different amounts. The unique qualities of each ingredient and the amount required in each recipe must be considered when selecting bulk storage and handling equipment.

Operator safety and ergonomics.

Operator safety and ergonomics.
The safety and well-being of personnel is a concern that spans all industries, including mix and blend manufacturing. To help keep employees safe and reduce the risk of ergonomic injuries and accidents, it is important to utilize semi- or fully-automated bulk ingredient handling systems that are easy to operate, troubleshoot, and maintain.
Bulk Ingredients for the Blend Plants Industry
-
Sugar
Sugar
Sugar
Sugar is an extremely common ingredient and often included in many bulk ingredient handling operations, such as snacks, mixes and blends, and candy confectionary. Whether it’s handled in a granular, crystalline form or as a powder, sugar is hygroscopic (which leads to clumping) and generates highly combustible dust. Careful consideration of these characteristics by AZO’s design and engineering team ensures the design of a bulk sugar handling system that delivers safe, reliable flow.
-
Bits, Morsels, Inclusions
Bits, Morsels, Inclusions
Bits, Morsels, Inclusions
Bits, morsels, and inclusions are the large, identifiable ingredients often used in manufacturing food such as snacks, candy confectionary, and mixes and blends. Inclusions are often explicitly advertised on product packaging, so their presence is both expected and verified by consumers. Frequently sticky, prone to clumping, or easily crumbled or broken (friable), bulk ingredient handling of bits, morsels, and inclusions requires a high degree of expertise. Careful consideration of each ingredient’s unique characteristics ensures the bulk handling system delivers consistent, reliable flow that addresses the challenges of bits, morsels, and inclusions.
-
Milk/Cheese Powder
Milk/Cheese Powder
Milk/Cheese Powder
Depending on their source — either animal or vegetable — milk and cheese powders have either high fat or high protein content. Either way, milk and cheese powders complicate bulk material handling. Whether they’re used in producing snacks, mixes and blends, or candy and confections, ensuring their smooth flow through a process is key to effective bulk handling. Maintaining proper environmental conditions prevents the separation or loss of fats, while proper dust mitigation minimizes explosion risks. Beyond managing unique ingredient characteristics, dry bulk handling systems must also provide dependable first-in/first-out flow to maximize product freshness, maintain batch control, and preserve hygienic conditions. AZO’s design and engineering team will deliver the dry bulk ingredient handling solution that safeguards product purity for any milk or cheese powder.
-
Mixes & Blends
Mixes & Blends
Mixes & Blends
Using mixes and blends as ingredients to produce snacks, candy confectionery, or baking mixes and blends, requires several considerations to ensure the mix remains blended through production and packaging processes. The key to their effective bulk handling is in the engineering and design of an automated bulk process solution. The system must accommodate the unique characteristics of each mix or blend to prevent it from separating into its component parts. Dry bulk handling systems must also maintain batch control, preserve hygienic conditions, and mitigate dust. Regardless of the recipe, AZO’s design and engineering team will deliver the dry bulk ingredient handling solution that safeguards product purity and consistency.
Sugar
Sugar is an extremely common ingredient and often included in many bulk ingredient handling operations, such as snacks, mixes and blends, and candy confectionary. Whether it’s handled in a granular, crystalline form or as a powder, sugar is hygroscopic (which leads to clumping) and generates highly combustible dust. Careful consideration of these characteristics by AZO’s design and engineering team ensures the design of a bulk sugar handling system that delivers safe, reliable flow.
Bits, Morsels, Inclusions
Bits, morsels, and inclusions are the large, identifiable ingredients often used in manufacturing food such as snacks, candy confectionary, and mixes and blends. Inclusions are often explicitly advertised on product packaging, so their presence is both expected and verified by consumers. Frequently sticky, prone to clumping, or easily crumbled or broken (friable), bulk ingredient handling of bits, morsels, and inclusions requires a high degree of expertise. Careful consideration of each ingredient’s unique characteristics ensures the bulk handling system delivers consistent, reliable flow that addresses the challenges of bits, morsels, and inclusions.
Milk/Cheese Powder
Depending on their source — either animal or vegetable — milk and cheese powders have either high fat or high protein content. Either way, milk and cheese powders complicate bulk material handling. Whether they’re used in producing snacks, mixes and blends, or candy and confections, ensuring their smooth flow through a process is key to effective bulk handling. Maintaining proper environmental conditions prevents the separation or loss of fats, while proper dust mitigation minimizes explosion risks. Beyond managing unique ingredient characteristics, dry bulk handling systems must also provide dependable first-in/first-out flow to maximize product freshness, maintain batch control, and preserve hygienic conditions. AZO’s design and engineering team will deliver the dry bulk ingredient handling solution that safeguards product purity for any milk or cheese powder.
Mixes & Blends
Using mixes and blends as ingredients to produce snacks, candy confectionery, or baking mixes and blends, requires several considerations to ensure the mix remains blended through production and packaging processes. The key to their effective bulk handling is in the engineering and design of an automated bulk process solution. The system must accommodate the unique characteristics of each mix or blend to prevent it from separating into its component parts. Dry bulk handling systems must also maintain batch control, preserve hygienic conditions, and mitigate dust. Regardless of the recipe, AZO’s design and engineering team will deliver the dry bulk ingredient handling solution that safeguards product purity and consistency.
AZO’s Bulk Ingredient Handling Solutions for the Mixes and Blends Industry: Outcomes & Benefits
With an AZO bulk ingredient handling system, your mixes and blends manufacturing operation will:
- Maintain proper hygiene and eliminate cross-contamination risks with easy-to-clean equipment.
- Easily accommodate a broad range of bulk ingredient characteristics.
- Receive ongoing support in adapting to changing recipes and new ingredients.
- Safely contain dust and significantly reduce explosion risk.
- Consistently and accurately comply with government track-and-trace requirements.
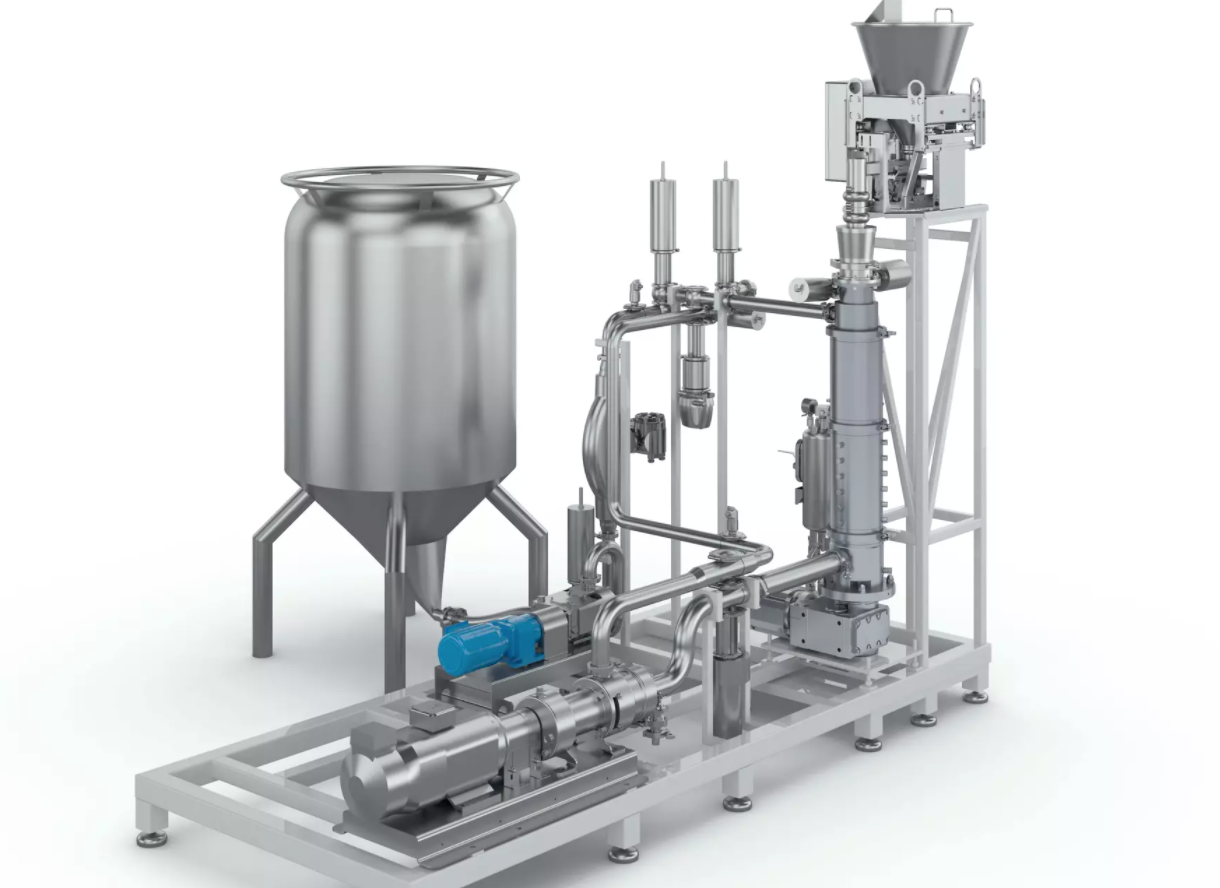