Sugar, being hygroscopic, will readily absorb moisture. In granular sugar, humid environments can result in clumps that resist flow. Powdered sugar, because of its fine texture, is extremely susceptible to clumping when exposed to moisture. When the proper environmental controls are not present, stored sugar can clump, stick, cake, or form bridges that prevent complete emptying of storage bins or bags. Providing the necessary equipment to control the environment around the sugar handling process is critical to optimize safe and reliable bulk flow.
Bulk Sugar Handling Solutions
It may taste sweet, but sugar’s attributes can make handling it a sour experience without experienced design and engineering to create a safe and reliable bulk handling system.
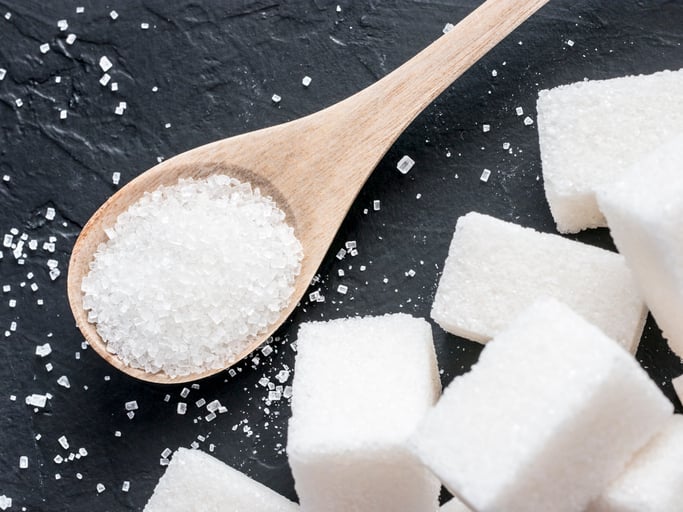
Bulk Sugar Handling: Overview
Sugar is an extremely common ingredient and often included in many bulk ingredient handling operations, such as snacks, mixes and blends, and candy confectionary. Whether it’s handled in a granular, crystalline form or as a powder, sugar is hygroscopic (which leads to clumping) and generates highly combustible dust. Careful consideration of these characteristics by AZO’s design and engineering team ensures the design of a bulk sugar handling system that delivers safe, reliable flow.
Bulk Sugar Handling: Common Challenges

Sugar requires a cool, dry environment.

Sugar requires a cool, dry environment.

Granular sugar has a high bulk density.

Granular sugar has a high bulk density.
Granular sugar has heavier bulk density and is more abrasive than many other powdered materials, such as flour. Granular sugar packs together more efficiently than powders, meaning in a given space there will be a greater quantity of it. Likewise, granular sugar has an abrasive texture, but it is fragile. If you aren’t careful when handling or conveying granular sugar, it could quickly become powdered sugar. Sugar’s abrasive characteristics will also wear out conveyor lines and receivers surprisingly fast. When designing a bulk handling system for sugar, it is critical to consider these characteristics.

Sugar is prone to explosion.

Sugar is prone to explosion.
Despite well publicized explosions at sugar processing plants — including Domino Foods’ plant in Maryland and Imperial Sugar’s factory in Georgia — many engineers continue to underestimate sugar’s explosive threat. Improper handling of granular or powdered sugar will generate high volumes of dust, which further heightens the risk of combustion. Even in a perfect situation, good material handling designs must include proper venting and explosion control. Every bulk sugar handling system must incorporate explosion protection and dust mitigation equipment to safeguard an operation and its employees.

Bulk sugar handling requires space for explosion protection.

Bulk sugar handling requires space for explosion protection.
Any bulk sugar handling operation must ensure adequate space for the installation of explosion protection and dust mitigation equipment. This may require some creativity in design and installation to ensure that necessary protection can fit into the available square footage — or be located in proximity to an exterior wall or roof — for venting. This can be especially challenging when adding explosion protection in an existing manufacturing plant.

Powdered sugar has unique handling needs.

Powdered sugar has unique handling needs.
Powdered sugar amplifies the problems with granulated sugar multi-fold. In its powdered form, sugar poses several unique handling challenges. Due to its hydroscopic nature, powdered sugar resists mass flow. Therefore, it should not be stored in large quantities. Even then, discharging and conveying powdered sugar requires specific equipment and processes. Small receivers should have a bottom vibrator to promote flow. In many cases, a mechanical agitating hopper designed for powdered sugar will be necessary. Additionally, powdered sugar’s fine particles can quickly accumulate and clog normal filters, so specialized filtration systems are also recommended.

Handling bulk sugar requires proactive dust mitigation.

Handling bulk sugar requires proactive dust mitigation.
The high volumes of dust generated by sugar are prone to ignition and a source of pest infestation. Explosion protection requires either suppression or venting to the outside the facility. Fugitive dust in a food plant is also an open invitation to unwanted pests. This is an especially troublesome problem in hard to reach or hidden areas. Every bulk ingredient handling system must incorporate explosion protection and dust mitigation equipment to safeguard a bulk sugar handling operation and its customers.
AZO’s Bulk Sugar Handling Systems: Outcomes & Benefits
AZO’s experienced design engineers understand the unique properties of granular and powdered sugar. Every bulk ingredient handling system we design incorporates equipment and solutions that reliably and effectively address the challenges outlined above. As a single-source provider of automated ingredient system equipment, AZO designs and engineers bulk sugar handling solutions that enhance both safety and productivity in your facility.
With an AZO bulk sugar handling system, your operation will:
- Avoid plugged or clogged silos to prevent downtime spent manually breaking up clumps.
- Convey sugar safely and effectively to promote smooth flow.
- Safely contain dust and reduce explosion risk.
- Sift out unwanted foreign material upon receipt and prior to dispensing.
- Optimize uptime with equipment that is easy to clean and inspect.
Questions About Bulk Ingredient Handling?
AZO’s Bulk Sugar Handling Systems: Equipment & Engineering Solutions
AZO has years of experience creating sugar handling systems with unique, engineering-centric designs. Your solution will match your unique requirements and be optimized for the safest, most reliable handling process. Each system AZO engineers for automated bulk dry ingredient handling of sugar includes: