Automated Ingredient Dosing
Introduction
Ingredient dosing systems for dry bulk ingredients are designed to accurately measure and weigh large quantities of materials, including powders. They are used in various industries, such as food processing, pharmaceuticals, and chemical manufacturing. These systems ensure precise and consistent dosing — also known as feeding — to reduce waste, boost accuracy, and improve efficiency in production processes.
Benefits of Using Ingredient Dosing Systems
More Efficient and Accurate Dosing of Ingredients
Recipes and formulations typically require a large number of ingredients, each in a unique amount. The optimal dosing system accommodates a range of ingredient volumes, including bulk (large amounts), minor (average amounts), and micro (small amounts). This enables accurate weighing across a wide range of volumes.
Automated ingredient dosing systems not only save time, but also reduce the risk of human error in measuring and dosing. The system can be programmed to dispense precise amounts of ingredients, ensuring consistency in product quality while reducing waste.
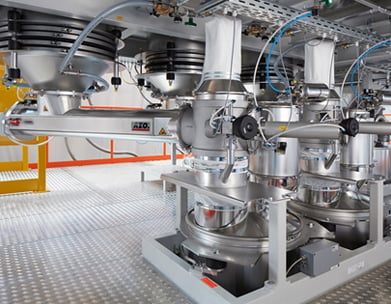
Ability to Handle a Wide Range of Ingredients
Whether it is powders, granules, liquids, or even sticky or cohesive materials, a well-designed dosing system can accommodate a wide variety of ingredients. This versatility is particularly beneficial for production lines that require multiple ingredients to be dosed simultaneously or for dosing of bulk, minor, or micro quantities. The ideal dosing system is customized to handle different recipes and adjust dosing quantities as needed, providing flexibility in production processes
Cleaner and Safer Working Environment
By eliminating the need for manual handling and measuring of ingredients, automated ingredient dosing systems reduce the risk of spills, contamination, and exposure of personnel to hazardous materials and fugitive dust. When designed with appropriate safety features — such as dust control or explosion suppression — the system ensures compliance with health and safety regulations.
Factors to Consider When Choosing an Ingredient Dosing System
Accuracy and Precision
The bulk ingredient dosing system should be able to dispense the desired quantity of ingredients consistently and accurately. This ensures that each weighment meets the required specifications of every product made on a given production line. Precise dosing is particularly important in industries such as pharmaceuticals or food processing to maintain consistent product quality and consumer safety.
Flexibility and Adaptability
Different products may require different dosing methods, such as volumetric or gravimetric dosing. The ideal system should be capable of accommodating various dosing techniques to cater to the specific needs of each ingredient. Additionally, the system should be able to handle different batch sizes and production volumes as required by throughput demands, while providing the necessary scalability for future growth or new products.
Reliability and Durability
The system should be built with high-quality materials and components that can withstand the demands of continuous operation and harsh working environments. It should also have built-in safety features to prevent any potential accidents or hazards during loading or dosing processes. Further, it should be easy to inspect and clean to ensure long-term reliability and durability.
Compatibility with System and Components
Ingredient dosing systems should be compatible with other equipment and processes in the production line. They should also be isolated from vibration or movement that will compromise the weighing and dosing process. The dosing system and its software should seamlessly integrate with existing machinery and control systems to enable synchronized operation, ingredient tracking, and batch control. Compatibility with industry standards and regulations is also crucial to confirm appropriate compliance and avoid any legal or regulatory issues.
Questions About Dosing System Design?

AZO’s Ingredient Dosing Systems
Volumetric Dosing Systems
AZO’s Volumetric Dosing System uses volumetric measurements — such as liters or gallons — to accurately dispense bulk ingredients. These systems typically consist of a hopper or container that stores the bulk ingredient and a dosing device. The dosing device can then discharge directly into a processing machine or bin which, in turn, feeds a conveyor line that transports the ingredient to the desired destination. AZO’s Volumetric Dosing System can be set to dispense a specific volume of the ingredient, ensuring precise dosing for each batch of production.
Gravimetric Dosing Systems
AZO’s Gravimetric Dosing System uses weight measurements — such as pounds or kilograms — to accurately dispense bulk ingredients. It typically consists of a scale or load cell that measures the weight of the ingredient and a dosing device. The dosing device can then discharge into a mixer or bin which, in turn, feeds a pneumatic conveying line. AZO’s Gravimetric Dosing System allows for more precise dosing than volumetric dosing, as it accounts for variations in the bulk ingredient’s density and moisture content.
Micro Dosing Systems
AZO’s Micro Dosing Systems for bulk ingredients accurately measure and dispense small quantities of ingredients comprising less than 5% of a given recipe or formulation. These systems utilize advanced technology and automation to ensure precise (down to single grams) and consistent dosing, reducing the risk of human error or dosing inaccuracies. By enabling precise control over ingredient quantities, AZO’s Micro Dosing Systems optimize production processes, minimize waste of high-cost ingredients, and maintain consistent product quality. They handle a wide range of bulk ingredients — from powders and granules — and are designed specifically for each micro ingredient used in the manufacturing process.
Gain-in-Weight and Loss-in-Weight Dosing Systems
AZO’s dosing systems can incorporate either a gain-in-weight or a loss-in-weight gravimetric feeder.
Gain-in-weight feeders dose material by weighing discrete amounts of each product on a scale into which the material is dispensed. Slower but more accurate, gain-in-weight feeders can only weigh one product discharged into one scale at a time. The term “gain-in-weight” refers to the increase in weight of the destination receptacle (typically a hopper or other container) as additional ingredients are added to it.
Loss-in-weight feeders continuously measure and dose material based on the weight that is removed from the storage bin. Typically faster, the loss-in-weight feeders allow for simultaneous discharge of multiple ingredients, as each feeder has its own scale. The term “loss-in-weight” refers to the decreasing weight of the product in the feeder container, which will diminish as its contents are dispensed into a receptacle.
Trust AZO for Your Ingredient Dosing Needs
AZO specializes in providing innovative solutions for bulk ingredient dosing systems. Designed to handle a wide range of ingredients — including powders, granules, and liquids — these dosing systems are both accurate and efficient. AZO's Bulk Ingredient Dosing Systems are highly customizable and can be tailored to meet the specific needs of any industry, including food and beverage, pharmaceuticals, chemicals, and plastics.
Equipped with advanced, high-precision weighing scales or load cells, AZO’s Bulk Ingredient Dosing Systems ensure accurate and consistent dosing of ingredients. The scales are designed to ensure accurate dosing, no matter the ingredient or the required weighments. Dosing systems can handle large quantities of ingredients and can be integrated with automated controls for seamless operation. The weighing technology is enhanced by advanced software that allows for real-time monitoring and dosing parameter adjustments. This produces precise dosing, even for challenging ingredients, every time.
By investing in an automated ingredient dosing system from AZO, manufacturers can ensure high product quality through consistent, repeatable, and reliable measurement.
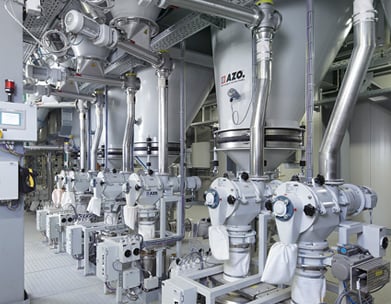
Schedule a Meeting to Discuss Dosing Systems
Resources About Dosing Systems
Solutions
AZO Dosing Screw
For continuous and discontinuous conveying and metering of various kinds of bulk materials, these units can be used in the food, plastics, chemical, and pharmaceutical industries.