Bulk Ingredient Control Automation
Table of Contents
Introduction
The terms “controls" and “automation" are closely related and often used interchangeably. At AZO, we prefer not to use them this way, as each has specific functions related to plant processes.
- Automation refers to anything that replaces human labor with a “machine” that automates the function. This machine requires a combination of mechanical, electrical, and electronic components.
- Controls are the electrical components (such as the motors) and electronic components (such as the programming software) that direct the operation of the machine.
For this reason, AZO considers controls to be a subset of automation. Automation always reduces the direct labor costs required to make saleable products by using an automated machine to perform tasks that otherwise would be handled by humans. These operational savings are offset by higher capital costs when the automation is installed.
Bulk ingredient control automation complements a mechanical material handling system by providing a level of accuracy and traceability unattainable with manual operations. For example, ingredient weighments and lot tracking are two functions more accurately performed by machines than humans over the course of thousands of repetitions. (AZO’s controls partner, Bachelor Controls, recently wrote about the benefits of preweigh automation). Without a fully integrated control system, a processing operation won’t have the verification it needs to ensure that the correct ingredients, in the proper amounts, are included in every batch of each type of product produced.
Modern bulk ingredient control automation systems provide operators with real-time feedback on a wide range of concurrent processes and functions. Material handling systems include hundreds of components working in a multitude of locations throughout a manufacturing plant, linked together in a common operating system and database. Control automation coordinates processing steps, creates a digital record of all activity, and can detect and adjust for environmental changes (such as temperature or humidity) to ensure the consistency of manufactured products. Consistent product quality avoids scrap losses by reducing the risk of bad batches, out-of-spec recipes, and even product recalls.
Benefits of Bulk Ingredient Control Automation
Minimized Downtime and Bad Product Batches
A bulk ingredient control automation system decreases the amount of defective or off-spec product manufactured. With a fully integrated control automation system, batch data is stored and analyzed in real-time, enabling faster variance detection. Plant managers, supervisors, and operators are notified of the problem and can quickly make the appropriate adjustments to mitigate production inconsistencies. This, in turn, reduces out-of-spec material and increases the overall efficiency of production systems. Control automation maintains the manufacturing quality and consistency expected by consumers.
Visual presentation of data to an operator also helps communicate the problem and provides diagnostic troubleshooting to fix the problem. Human machine interface (HMI) systems alert operators about issues in a clear and concise manner so they can identify and resolve problems quickly. Electronic data analysis of batches can detect product problems significantly faster than manual data oversight. Further, monitoring mechanical equipment issues can help operators address them promptly, preventing catastrophic failures, wasted product, and lost productivity.
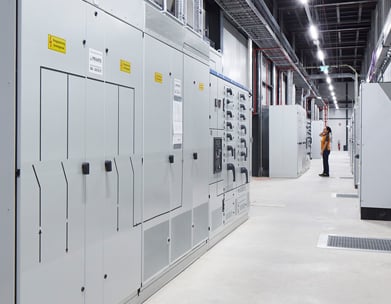
Increased Traceability
Historically, clipboards and manual observation were the primary means to record data on-site. This is inherently flawed compared to control automation. Integrated control systems record production data electronically. This avoids manual data input and inevitable typographic errors. Barcoding ingredients allows the machine to confirm and interact with the operator to verify the right ingredient has been measured to the precise amount required by the recipe.
Automated processes can be easily audited, which ensures superior record keeping and more reliable production results. This, in turn, makes compliance with regulatory agencies — if required of a manufacturer — much easier. With a fully automated system, a manufacturer gets complete product and batch genealogy, all stored electronically and easily accessible. This is particularly helpful when reporting to the Food and Drug Administration (FDA) or other regulatory agencies.
Advanced manufacturing control systems in the food and pharmaceutical industries help to avoid product recalls and meet required verification processes. Information stored electronically can be backlogged, saved for years, and retrieved quickly. This facilitates reporting for the FDA’s Food Safety Modernization Act (FSMA), which requires companies to “shift focus from responding to foodborne illness to preventing it.”
In the pharmaceutical world, 21 CFR part 11 requires companies to validate electronic systems for quality and compliance. Bulk ingredient control automation ensures effective track and trace of each specific product. It documents not only to the batch level, but also down to pallets, cases, and even individual cartons of each ingredient used to manufacture the product. Variances and other anomalies can be easily spotted and analyzed, leading to faster decision making. Production can then be adjusted or stopped faster, halting the manufacture of an out-of-spec product and reducing the probability of product recalls.
Improved Work Conditions
Manufacturing plants tend to put their best people in the most critical roles. But that isn’t enough to prevent human errors. Further, with today’s limited labor availability, the long-standing challenge of finding enough workers to staff all the production shifts has become even more difficult. Automation addresses both issues.
Bulk ingredient handling systems directed by control automation reduce direct labor costs. They also support safer work environments and eliminate repetitive injuries. High labor turnover is often driven by working conditions. Turnover requires more overtime — or requires new, untrained people — to achieve adequate staffing. More overtime increases labor costs, while unfilled positions can shut down a production shift.
Further, robotic automation performs monotonous, low skill tasks around the clock, preventing workers from sustaining repetitive motion injuries and freeing them to handle more value-added tasks. European companies are way ahead of American companies in their use of automation to reduce labor costs in many manufacturing plants.
Another staffing issue facing manufacturers is the aging and evolving workforce. These more mature, hig-value employees will eventually retire and must be replaced with a younger generation. During this generational transition, it’s critical to find a way to retain the institutional knowledge associated with a piece of equipment or process. Otherwise, it will be lost when senior employees retire and are replaced by younger, less experienced staff members. Bulk ingredient control automation systems offer a reliable, permanent means to institutionalize critical production processes without relying on the individuals doing the job.
Accuracy and Return On Investment
Generally, a higher level of accuracy is more expensive than a lower standard of accuracy. This should always be kept in mind when considering a bulk ingredient control automation system. An overly stringent specification requirement can cause capital costs to escalate unnecessarily, significantly reducing the overall return on investment (ROI). For example, a 5,000-pound weighment for one ingredient with 2-gram accuracy would be both expensive and unnecessary. A more reasonable specification would be to ensure all weighments are within 99.8% accuracy (or +/- 10 pounds in this example). This accuracy target would apply to all ingredient weighments required for any recipe.
To ensure the optimal balance between accuracy and ROI, it’s important to evaluate the overarching control automation goals for the process. Depending on the extent of the desired automation — the entire facility, a single manufacturing line, or the dosing of one class of ingredient — the desired degree of accuracy may vary.
It can often be helpful to first assess current cost drivers (such as scrap, rework, or workers compensation claims) to help identify problematic production areas when prioritizing automation solutions. While there are many factors that could influence the cost of bulk ingredient control automation, the ideal system will deliver improved throughput, product quality, process efficiency, and operator safety for years after the initial purchase.
Factors to Consider when Choosing Bulk Ingredient Control Automation
Compatibility with Existing Systems and Equipment
Compatibility with existing systems and equipment is of utmost importance when choosing a bulk ingredient control automation. This compatibility ensures a seamless integration of the new automation system into the existing infrastructure, minimizing disruptions and facilitating a smooth automation transition. By choosing a system that is compatible with the existing equipment, companies can avoid costly and time-consuming modifications or replacements. Compatibility also allows efficient utilization of existing resources and maximizes ROI. Ultimately, the compatibility of the automation system with existing systems and equipment enhances productivity, reduces downtime, and improves overall operational efficiency.
Scalability to Accommodate Future Growth
By investing in a scalable bulk ingredient control automation solution, companies can avoid the need for costly replacements or upgrades when new products are added or when the plant capacity is increased. It enables production processes to efficiently handle larger volumes, new ingredients, streamline workflows, and enhance productivity. Moreover, scalability supports flexible incorporation of new technologies and functionalities. This positions manufacturers to stay ahead of the competition, provide new products to customers, and meet all regulatory reporting requirements. Investing in a scalable solution gives a manufacturer the ability to future-proof operations, support consumer demand, and fuel company growth.
Integration Capabilities with Data Management Software
Assess the ability of a control system to seamlessly integrate with data management software. This allows for efficient and accurate tracking, monitoring, and analysis of ingredient usage and other production data. Such integration enables real-time visibility into inventory levels, batch tracking, and production data. It also optimizes control over ingredient usage and minimizes off-spec scrap. Additionally, integration with data management software facilitates easy reporting and compliance with regulatory requirements, streamlining operations and avoiding product recalls.
User-Friendly Interface and Ease of Implementation
Specify a user-friendly human machine interface (HMI) to ensure that operators can easily navigate and interact with the system. This allows humans and machines to work together to increase efficiency. The optimal HMI provides quick, intuitive access to errors and other information, enabling operators to make informed decisions and take corrective actions promptly. Additionally, control systems can help train new operators, supporting a smooth transition from manual to automated processes while minimizing disruptions and downtime due to operator confusion.
Questions About Bulk Ingredient Control & Automation?
AZO’s Bulk Ingredient Control Automation Solution
A sophisticated and effective AZO Bulk Ingredient Control Automation solution will perform the following functions:
- Track and trace accurately and effectively
- Create safer, more ergonomic working environments for employees
- Ensure the correct amount of all ingredients in each batch every time
- Mitigate human error in production processes
- Reduce repetitive injury costs
- Offer flexible alternatives to expanding processes with pieces of automation
- Support a comprehensive, interlaced batch production system
- Provide independent master data management
- Document, record, and store operating steps and weighing results
The majority of AZO’s automated control systems are supplied by our partner, Bachelor Controls Inc. (BCI). The AZO/BCI partnership goes back nearly 30 years, resulting in hundreds of reliable, user-friendly automated control systems.
BCI is a leading provider of control system solutions to manufacturers in the food processing, pet food, pharmaceutical, plastics, specialty chemicals, and industries. The company's controls specialties include high-end batching systems, extrusion feeding, automated bulk material transport, and other material handling.
The BCI team brings tremendous expertise in designing, building, and installing integrated control systems for automated material conveying systems. Experts in manufacturing execution systems (MES) solutions, BCI’s solutions integrate process control systems with enterprise resource planning (ERP) systems to give operations real-time information they can use to make critical business decisions quickly.
Trust AZO for Your Bulk Ingredient Control Automation Needs
AZO’s Bulk Ingredient Control Automation plays a vital role in enhancing the efficiency and quality of production processes in various industries. By implementing state-of-the-art control systems, companies can ensure consistent and accurate measurements of ingredients, reducing the risk of errors and inconsistencies.
Control automation from AZO can streamline the manufacturing process by automating tasks such as weighing, recording, and dispensing — eliminating the need for manual intervention. This not only saves time but also minimizes the chances of human error. Additionally, AZO’s bulk ingredient control automation systems enable companies to maintain precise inventory management. This ensures that the right amount of ingredients is always available, reducing waste and costs.
By investing in control automation from AZO, manufacturers can significantly improve productivity, quality, and cost-effectiveness.
Resources About Bulk Ingredient Control & Automation
Solutions
AZO Rolog
The AZO Rolog uses a robot to dose an extremely variable number of micro quantities (up to 10 kg) in a fully automated process.