Engineered for precision and efficiency, pneumatic conveying of bulk ingredients utilizes the force of air or specialty gas to move bulk materials through intricate pipelines from delivery to storage to production.
Bulk Ingredient Handling in the Plastics Industry
Rely on AZO to engineer durable, reliable, and accurate bulk ingredient handling systems that ensure your plastics manufacturing process delivers consistent and exacting products.
Bulk Ingredient Handling for the Plastics Industry: Overview
Plastic formulations must match the exact standards required across the broad range of plastic products available today. Further, the plastics manufacturing industry demands a high level of process accuracy. To meet your blend formula’s standards, AZO’s bulk ingredient handling systems precisely measure and dispense resins, TiO2, fumed silica, modifiers, stabilizers, additives, fillers, and minor ingredients into extruders and molding machines to match the exact product formulation. Rely on AZO’s engineering-centric experience in the plastics industry to deliver the optimal bulk ingredient handling solution that combines safety, accuracy, and reliability.
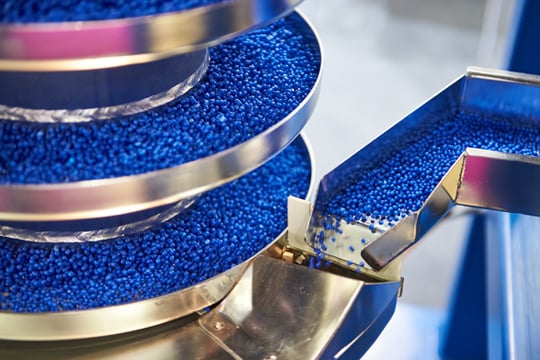
Typical Plastics Industry System

Heater / Cooler Mixer (Buyout Equipment)
Vacuum Passthrough Receiver
Rotary Valve (Buyout by AZO)
Product Intermediate Storage Vessels
AZO offers a comprehensive range of bulk ingredient storage systems tailored to meet the distinct needs of different materials and manufacturing processes.
Vacuum Pump (Buyout by AZO)
Control System
AZO’s Bulk Ingredient Control Automation plays a vital role in enhancing the efficiency and quality of production processes in various industries.
Vacuum Receiver
Secondary Air Filter
Product Packaging Machine (Provided by Customer)
Bulk Ingredient Handling for the Plastics Industry: Common Challenges

Proper and timely introduction of ingredients into the extruder or molding machine.

Proper and timely introduction of ingredients into the extruder or molding machine.
Before extruder systems can produce high-quality plastic products, weighing and dosing equipment must accurately measure and precisely dispense the appropriate quantities of ingredients. These include modifiers, stabilizers, additives, and fillers. Plastic manufacturers must utilize reliable equipment that ensures the final product matches required specifications, day-in and day-out.

Precisely controlled dispensing of additives to extruders.

Precisely controlled dispensing of additives to extruders.
Consistent plastic colors are critical for long-term success in the plastic industry. This requires precise dosing of both colors and additives. Often dispensed in small amounts, dependable dosing of additives and colors is necessary to achieve plastic product consistency.

Storing and utilizing regrind in a manufacturing process.

Storing and utilizing regrind in a manufacturing process.
With both environmental sustainability and waste reduction in mind, many plastic manufacturers incorporate as much regrind material as possible in their formulations. It is important to create a regrind handling system that can store, convey, and dispense a consistent amount of material back into the production extruder.

Plastics manufacturers must properly handle hazardous materials.

Plastics manufacturers must properly handle hazardous materials.
Liquid plasticizers and other chemicals used in plastic production must be safely stored, dispensed, and conveyed within an operation. Equipment must be capable of completely containing all hazardous materials to safeguard the health and well-being of employees and to minimize insurance risks.

Plastics manufacturers must contain dust.

Plastics manufacturers must contain dust.
A method for containing the high volumes of dust generated by many ingredients used in plastic manufacturing should be included in every bulk material handling system design. Fugitive dust can lead to any number of problems, including operator exposure, or in the worst case, ignition. Improper dust control creates an unsafe working environment for personnel and increases the risk of combustion.

Bulk ingredient handling requires space for explosion protection.

Bulk ingredient handling requires space for explosion protection.
Bulk ingredient handling systems must include appropriate explosion protection and dust mitigation equipment. This is especially important when upgrading legacy systems, which may require some design creativity to ensure that necessary protection can fit into the available space.
Bulk Ingredients for the Plastics Industry
-
TiO2
TiO2
TiO2
Bright white and used in a variety of everyday products, TiO2 is an extremely common ingredient in many bulk ingredient handling operations, including personal products, poly and plastics, chemicals, and pharmaceuticals. Characterized by fine particles that flow poorly, TiO2 is moderately abrasive and forms heavy, dense clumps. These critical attributes can make emptying this ingredient out of storage vessels or successfully conveying it challenging. AZO’s engineering team carefully considers each of these factors to ensure the design of a TiO2 handling system is safe, reliable, and dust free.
-
Resin
Resin
Resin
Incorporated into a variety of products in unique and exacting formulations, resin is a diverse ingredient category that includes applications in PVC dry blends, plastics, and chemicals. Further, it is often toxic and generates highly combustible dust. These critical attributes can make successfully conveying it safely and without clogs challenging. AZO’s engineering team carefully considers each of these factors to ensure the design of a bulk resin handling system is safe, reliable, and dust free.
-
Diatomaceous Earth
Diatomaceous Earth
Diatomaceous Earth
A type of crystalline silica made from pulverized sedimentary rock, diatomaceous earth comes in many forms, including pellets, particles, or powder. In its powdered form, this naturally occurring ingredient has a high surface area and light density. It is an ingredient used in a range of beverage and food grade filtration applications and in many industrial applications. Whether it’s used in manufacturing of personal products, pharmaceuticals, chemicals, or beverage filtration, diatomaceous earth powder’s unique characteristics require special material handling solutions. It is prone to producing high amounts of dust, which is a carcinogen. AZO’s engineering team carefully considers each of these factors to ensure the design of a diatomaceous earth handling system is safe, reliable, and dust free.
TiO2
Bright white and used in a variety of everyday products, TiO2 is an extremely common ingredient in many bulk ingredient handling operations, including personal products, poly and plastics, chemicals, and pharmaceuticals. Characterized by fine particles that flow poorly, TiO2 is moderately abrasive and forms heavy, dense clumps. These critical attributes can make emptying this ingredient out of storage vessels or successfully conveying it challenging. AZO’s engineering team carefully considers each of these factors to ensure the design of a TiO2 handling system is safe, reliable, and dust free.
Resin
Incorporated into a variety of products in unique and exacting formulations, resin is a diverse ingredient category that includes applications in PVC dry blends, plastics, and chemicals. Further, it is often toxic and generates highly combustible dust. These critical attributes can make successfully conveying it safely and without clogs challenging. AZO’s engineering team carefully considers each of these factors to ensure the design of a bulk resin handling system is safe, reliable, and dust free.
Diatomaceous Earth
A type of crystalline silica made from pulverized sedimentary rock, diatomaceous earth comes in many forms, including pellets, particles, or powder. In its powdered form, this naturally occurring ingredient has a high surface area and light density. It is an ingredient used in a range of beverage and food grade filtration applications and in many industrial applications. Whether it’s used in manufacturing of personal products, pharmaceuticals, chemicals, or beverage filtration, diatomaceous earth powder’s unique characteristics require special material handling solutions. It is prone to producing high amounts of dust, which is a carcinogen. AZO’s engineering team carefully considers each of these factors to ensure the design of a diatomaceous earth handling system is safe, reliable, and dust free.
AZO’s Bulk Ingredient Handling Solutions for the Plastics Industry: Outcomes & Benefits
With an AZO bulk ingredient handling system, your plastics manufacturing operation will:
- Ensure product consistency and quality via highly accurate automatic weighing and dosing of bulk ingredients.
- Easily accommodate a broad range of plastics formulations and ingredients.
- Safely contain dust and hazardous chemicals to significantly reduce explosion risk.
- Keep employees safe by reducing ergonomic injuries and accidents.
- Significantly cut costs through effective use of regrind and reduced scrap.
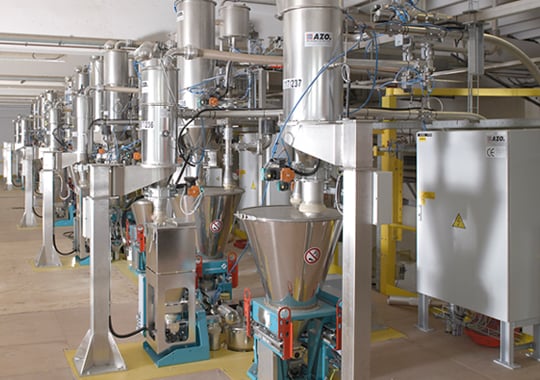
AZO’s Bulk Ingredient Handling Systems for the Plastics Industry: Equipment & Engineering Solutions
Questions About Bulk Ingredient Handling?
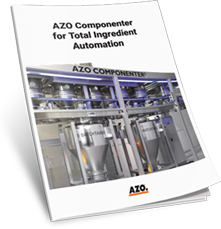