Bulk Ingredient Storage
Introduction
As manufacturers navigate production, the seamless and strategic management of raw materials in the manufacturing plant is of high importance. Bulk ingredient storage involves the safe and systematic handling and storage of essential materials that comprise various products.
Powdered materials can have very different characteristics which require different storage vessels in a range of sizes, shapes, and capacities. Silos, bins, hoppers, and tanks all play crucial roles in streamlining the supply chain and supporting production. They’re also important for optimizing operational workflows, maintaining product quality, and bolstering overall manufacturing efficiency. Choosing the right combination of bulk ingredient storage systems ensures material availability while avoiding production bottlenecks to optimize a manufacturing process.
Benefits of Bulk Ingredient Storage
Streamlined Material Handling
Bulk ingredient storage solutions enhance material flow through strategic placement, controlled discharge, and efficient retrieval mechanisms. These systems are initially used when raw material enters the manufacturing plant. Bulk or bagged materials must first be unloaded or emptied into intermediate storage bins or silos. These storage vessels are connected to the processing equipment to support automated material handling. For maximum operational efficiency, the storage vessels streamline ingredient handling while minimizing disruptions and optimizing production timelines.
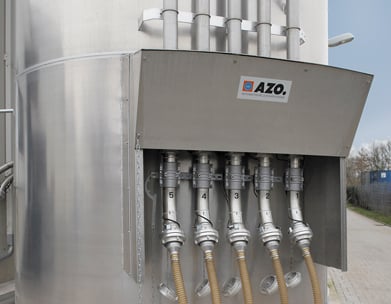
Enhanced Product Integrity
Tailored to meet specific material characteristics and requirements, bulk ingredient storage solutions should continuously measure the amount of product at each storage location. They should also protect ingredients from being compromised, damaged, or contaminated. This ensures the manufacture of end products that meet stringent quality standards.
Seamless Operational Continuity
To support operational continuity, bulk ingredient storage solutions ensure material is available when needed. This includes scales in the storage bins and electronic record keeping that tracks the amount of each ingredient in the system. With the ability to store large volumes of ingredients and access real-time data, an operation can avoid production interruptions and maintain seamless workflows.
Optimization of Available Space
Bulk ingredient storage solutions enhance space utilization by leveraging both vertical and horizontal square footage. In manufacturing facilities where real estate is at a premium, these solutions optimize the cube of the building to fully maximize its available space. Pneumatic conveying can also separate material unloading — which is both inherently dusty and space consuming — from the production and processing operation.
Factors to Consider when Choosing Bulk Ingredient Storage
Material Characteristics
The unique attributes of the materials to be stored — from flow behavior to moisture sensitivity — must be considered when determining the most appropriate storage solution. For example, the shape of the bin bottoms can facilitate efficient discharge. Storage b
Storage Capacity
When evaluating the capacity of the different types of bulk ingredient storage systems, start with the recipe requirements for each product produced. Major ingredients require silos. Minor ingredients require small bulk bag or bag dump stations and bins. Micro ingredients can be stored in much smaller bins. It is also wise to keep both current and future production demands in mind to prevent production bottlenecks or allow for future growth.
Installation and Integration
Integrating new equipment or systems into existing operations requires both expertise and detailed planning. The selected solutions should seamlessly integrate into existing workflows to minimize downtime, enabling quick start-up and efficient material retrieval.
Spatial Optimization
Good design requires verification that the bulk ingredient storage systems under consideration will fit in available space, while allowing room for future expansion if necessary. Conveyor lines are necessary from each storage location to processing equipment. Their layout is determined by the physical means required to move the ingredients, as well as the pre-existing facility constraints along the route from storage to production.
Cleaning and Maintenance
Evaluate how easy it is to clean and maintain the storage solutions. Equipment that is easy to access for cleaning minimizes downtime and prevents cross-contamination. Keep in mind, hard to reach cleanout points will rarely be cleaned.
Safety Features and Compliance Standards
Depending on the materials stored and the production environment, there may be specific safety requirements or regulations governing the design of the bulk ingredient storage solution. Examples could include vibration equipment to ensure discharge, air conditioning to protect against moisture, or explosion protection for safety. Compliance with standards set by regulatory bodies and industry organizations is crucial to ensure that the equipment meets all necessary safety requirements and hygiene standards.
Questions About Bulk Ingredient Storage Systems?
AZO’s Bulk Ingredient Storage Systems
AZO offers a comprehensive range of bulk ingredient storage systems tailored to meet the distinct needs of different materials and manufacturing processes. Bulk materials are all unique and any bulk storage design should start with an in-depth analysis of each of the materials required in the design. Every AZO storage solution is engineered to optimize material handling, preserve product quality, maximize available space, and enhance operational efficiency of each material whose handling will be automated. All storage vessels should include scales which provide real-time data for the automated control system. AZO’s different types of bulk ingredient storage solutions include:
Silos
Robust and space-efficient, AZO’s silos provide vertical storage solutions for dry and free-flowing bulk ingredients. Crafted from a variety of high-quality materials, AZO silos ensure reliable storage while maintaining material integrity. Their design should also include the truck or rail car unloading equipment needed to fill the silo.
Bins
AZO's versatile bin solutions offer horizontal storage options, accommodating a wide range of materials including solids or granules. Bins are designed to optimize space utilization while enabling easy loading, either by bulk bag or super sack.
Hoppers
Engineered for controlled material discharge, AZO’s hopper systems seamlessly integrate into various production processes. With an AZO hopper, handling materials with challenging flow characteristics becomes effortless. Hoppers are generally used as temporary storage locations for materials or ingredients enroute from storage to production.
Tanks
For liquid and viscous materials, AZO offers tanks in various shapes and sizes, each equipped with features to ensure exacting storage and controlled processing. Customizable, these tanks can be engineered to meet specific temperature, agitation, and level control requirements.
Trust AZO for Your Bulk Ingredient Storage Needs
Whether storing dry powders, liquids, granules, or other bulk ingredients, AZO's diverse range of bulk ingredient storage systems can be tailored to meet specific recipe or production requirements. Leveraging AZO’s engineering expertise ensures a facility attains the storage solutions that integrate seamlessly into its production processes in the most cost-effective manner possible. This minimizes up-front capital cost and enhances productivity and quality assurance during operation and production.
By investing in a robust bulk ingredient storage system from AZO, manufacturers can improve material handling efficiency while optimizing production throughput and capacity.
Resources About Bulk Ingredient Storage
Reliable conveying
Perfecting Film Quality: How AZO Enhanced Consistency in the Safety Glass Industry
Following the successful implementation of AZO's silo blending capabilities, the "Glass Film Innovators" have enjoyed five years of consistent, high-quality film production ensuring that any variations in raw materials are thoroughly mixed, eliminating the risk of inconsistent film quality from the extruder.
Solutions
AZO Container Systems
The AZO container program ranges from the standard economy model to high-end designs to meet the highest demands in the food and pharmaceutical industry.