Bulk Ingredient Screening
Introduction
Bulk ingredient screening, often accomplished with vibratory or rotary screeners, is more than a mechanical operation. It's a prudent strategy that safeguards against product inconsistencies and production inefficiencies. By sifting out undersized or oversized particles — as well as foreign material — bulk ingredient screening favorably impacts the composition of the final product. From food to chemicals, screening ensures that each batch meets quality standards.
Bulk ingredient screening also serves as a preventive measure against downstream equipment wear and tear. By removing contaminants and irregularly sized particles at an early stage in the production process, screening extends the longevity of processing machinery, minimizing the risk of breakdowns and downtime. This proactive approach is particularly important for industries that rely on continuous production, as it mitigates disruptions and optimizes operational continuity.
Ultimately, bulk ingredient screening ensures material uniformity, enhances downstream equipment longevity, and helps to ensure product quality — all elements crucial for reliable operations and product quality in any industry.
Benefits of Screening Bulk Ingredients
Screeners ensure product integrity and operational efficiency by employing mechanical action to clean and condition bulk powders. Before going to production, bulk materials should be safety checked for unwanted contaminants which could compromise product integrity or equipment longevity. Product conditioning prevents lumped material from entering the product stream, improving mixing or extruding performance. These benefits cascade across industries, optimizing material handling with finesse.
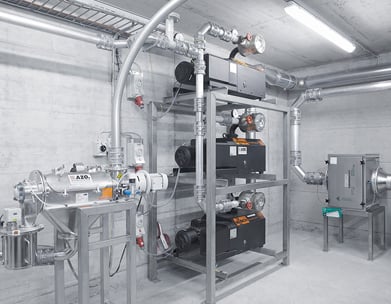
Material Preservation
Bulk materials should be delivered without any unexpected contaminants. However, the only way to ensure this is to include a safety step provided by screening. Screeners, which can be customized for specific materials, can be installed in the material flow to prevent bottlenecks or blockages. Their variable settings also safeguard material integrity during separation. This function is especially important in industries where maintaining product integrity is critical, such as in food or pharmaceuticals.
Particle Consistency
Screeners create uniformity in particle size distribution, an important aspect of effective mixing and extruding. By segregating particles based on size, screeners create homogeneous powders that can meet precise specifications. Large particles or agglomerated material that is too large to pass through the screen are discharged from the screener and recycled back to the screener inlet to be screened a second time. This ensures material consistency for efficient downstream processing.
Efficient Material Separation
Screeners enhance production speed by efficiently sorting particles by size. The process described above for deagglomerating clumps of material minimizes waste and maximizes throughput. The result is a consistently sized production flow that optimizes production operations.
Equipment Preservation
Screeners play a pivotal role in safeguarding downstream equipment by removing unwanted materials inadvertently delivered by vendors. Often seen in bulk powder deliveries, screeners can protect downstream equipment by catching wood, metal, or plastic. It seems hard to believe, but some manufacturers have discovered 2x4s or metal chain in rail car or truck deliveries. This proactive approach extends equipment lifespan and reduces downtime.
Factors to Consider when Choosing a Bulk Ingredient Screener
Material Characteristics
The distinctive attributes of bulk ingredients — such as particle size, shape, and moisture content — are important considerations when evaluating screener options. Screeners are designed to allow owners to install a wide range of screen mesh sizes as required for specific material properties. This ensures efficient and accurate separation while rejecting oversized material.
Throughput Requirements
Determining the required throughput capacity is key when sizing a bulk ingredient screener and selecting the optimal screen mesh size. Different size screeners are available to accommodate varying production volumes. Matching the screener's capacity with production demands prevents bottlenecks and optimizes operational throughput.
Particle Size Distribution
Target particle size distribution is another important factor that impacts screener choice. Some screeners are engineered to provide a single particle size pass through. Other screeners are designed with multiple screens which all for capturing multiple particle sizes. Matching the target particle size distribution goals with the screener’s capabilities is critical for achieving successive production objectives.
Material Flow
Efficient material flow into and through the screener is essential for optimal performance. High quality screeners have built-in feeders that can control the material inflow rate to prevent an excess amount of material from overwhelming the screening chamber. Factors like flow rate and material behavior influence bulk ingredient screener operation, effectiveness, and efficiency. Select a screener and screening media that matches the desired material flow rate and particle size characteristics to prevent clogs and bottlenecks in production.
Screen Mesh
The choice of screen mesh directly affects particle separation efficiency. Different bulk ingredients influence screen mesh size, as does the amount of material required to pass through the screener to production. The throughput capacity of any screener varies widely depending on both the material to be screened and the mesh size of the screen media. The selected screen mesh, as determined by the particle size specifications, generally dictates the physical size of the screener.
Maintenance and Accessibility
A screener's design should make maintenance and cleaning easy. It should allow quick access to screens and other internal components to ensure quick inspection and streamlined maintenance. Screens are wear parts and should be inspected regularly as part of normal operation. When using a single machine to screen different materials, an easy to swap screen cage allows for quick changeouts of different size screens.
Adaptability and Customization
Manufactured products evolve over time, as do production requirements. Opting for a screener with customizable settings and quick clean out provides maximum flexibility to support changing production needs and futureproofing.
Footprint and Space
Be sure to assess the available floor space and its overall dimensions when considering different screener sizes and options. Verifying that the chosen screener fits within the allocated space is essential for seamless integration of new equipment into existing manufacturing processes.
Questions About Bulk Ingredient Screening Systems?
AZO’s Bulk Ingredient Screening Systems
AZO offers several different types of precision engineered bulk ingredient screening systems. These solutions serve as gatekeepers, separating materials by particle size while enhancing product quality and production efficiency. Other screener types are available from other specialty vendors to accommodate diverse material characteristics and production requirements. AZO’s screeners include:
Centrifugal Screeners
AZO’s Centrifugal Screeners utilize centrifugal force in the screening chamber to propel particles outward to the surrounding screen. The mesh size of this screen allows acceptable particle sizes to pass out of the screener chamber. Oversized particles bounce off the screen and rebound back against the rotating agitator arms.
This process repeats until either the particle size is reduced enough to pass through the mesh, or larger particles pass out of the screening chamber to the “overs” bucket. This bucket can collect out-of-spec material, primarily when cleaning the product. Or the bucket’s contents can be returned to the screener inlet for a second round of processing, primarily when delumping the material.
These screeners excel in high-capacity, in-line applications where maintaining material integrity is crucial. The centrifugal mechanical action of the screener process self-cleans the screen mesh. This helps prevent clogging and a resulting decrease in throughput.
Vibratory Screeners
Vibratory screeners leverage oscillating motion to segregate particles based on size. Ideal for free-flowing materials, these screeners excel at efficiently separating particles into multiple distinct fractions. Their gentle material handling is offset by their inability to self-clean. They also require a large footprint due to the size of the machine and its physical motion.
Rotary Screeners
Rotary screeners, also known as trommel screens, employ rotating cylinders to separate particles. Rotary screeners are particularly adept at handling larger volumes and abrasive materials. With varying cylinder sizes and screen mesh options, these screeners are an optimal solution for applications where large throughput and maximum mechanical action are essential.
Gyroscopic Screeners
A specialized screener, they employ gyratory motion to achieve efficient particle separation. These screeners are best suited to applications requiring precise particle size control and low material flow. Their gentle yet thorough screening action makes them an optimal solution for handling fragile particles.
Trust AZO for Your Bulk Ingredient Screening System Needs
Bulk ingredient screening systems are a critical component in a variety of every industry where materials must be separated by particle size, or foreign materials effectively removed. Efficient screeners not only ensure product quality and consistency, but also contribute to process optimization and operational throughput.
AZO designs and engineers advanced bulk ingredient screening solutions to meet the diverse needs of many industries. AZO’s innovative screeners have been an industry leading technology for more than 75 years. Every AZO screener is backed by comprehensive technical assistance and support.
By investing in robust bulk ingredient screening systems from AZO, manufacturers can maintain their commitment to delivering high quality products while optimizing production processes.
Resources About Bulk Ingredient Screening
Solutions
SelectingThe Right Screener for Your Business
An engineers’ and executives’ guide to specifying, justifying and maintaining screening equipment for your operations.
AZO Screeners
AZO DA Screener
The multifunction machine for reliable, simultaneous safety screening, dosing, and precise weighing.
AZO Screeners
AZO FA Screener
The FA type of cyclone screener is directly used in the pneumatic conveying stream for safety screening and fractionating of material, for eliminating foreign matter, breaking lumps, and for lifting/loosening product.