Pneumatic Conveying of Bulk Ingredients
Introduction
Ideal for industries handling large volumes and where product purity is critical, bulk ingredient pneumatic conveying features non-contact transport methodology. By eliminating exposure to the hardware of mechanical conveying equipment, pneumatic conveying eradicates the risk of product contamination, degradation, or separation of materials during transit.
There are three basic types of pneumatic conveying commonly used for bulk materials. They are dilute phase, dense phase, and semi-dense phase. The optimal pneumatic conveying methodology depends on the physical characteristics of the materials the system will move.
- Dilute phase conveying employs a large amount of air at low pressure and high velocity to convey a small amount of material. It is ideal for non-fragile materials.
- Dense phase conveying uses a small amount of air at high pressure and low speed to convey large amount of material. It is suitable for heavy and large particles that are prone to breakage.
- Semi-dense phase conveying is a compromise between dilute and dense. It deploys a moderate amount of air at medium pressure to convey medium amounts of material.
Vacuum conveying has the inherent advantage of keeping the powder inside the pipes; any hole in the system pulls air from outside the system into the convey lines. In a pressure system, however, that same hole allows the moving powder to blow through it. This results in undesirable fugitive dust, often in hard to see or hard to clean areas. Conversely, pressure conveying does have a usable distance advantage of roughly 600 feet versus about 300 feet for vacuum conveying.
Additionally, both types of pneumatic conveyors transport materials across extensive distances while navigating complex routes to multiple destinations. This enhances efficiency by eliminating both multiple transfer points and intermediate storage. By streamlining the entire production process, pneumatic conveying optimizes workflows. It separates messy powder delivery from production areas and automates cumbersome transportation, which minimizes labor requirements and reduces material handling costs.
Benefits of Pneumatic Conveying
Fast, Efficient Transport
One of the biggest advantages of pneumatic conveying is its ability to transport bulk materials quickly and automatically. Compared to other methods of transportation — such as bucket elevators, manual transport, or screw conveyors — pneumatic conveying systems are much faster and can handle larger quantities of materials. Although the capital costs of pneumatic conveying systems are higher, they have much lower operating costs. This is especially important in industries with high production rates where downtime is exceptionally costly.
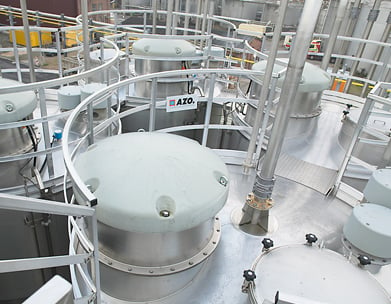
Flexibility
Engineers can design pneumatic conveying systems to fit specific plant layouts and production requirements. The use of valves and switching can allow a single storage location to serve multiple production lines in different locations within a manufacturing plant. This means that the system should be customized to fit the needs of a particular application. Whether transferring materials from one processing line to another, or delivering raw materials to a production line, a pneumatic conveying system can be custom engineered to match unique specifications.
Hygienic Safety
Pneumatic conveying systems are hygienic and safe. Since the materials are transported through a closed pipeline, there is no risk of contamination or spillage. They also operate with a minimum of moving parts, keeping workers safely away from moving equipment. Vacuum conveying also minimizes fugitive dust, while cost control and explosion protection are generally included in pneumatic conveying systems.
Cost Savings
Pneumatic conveying systems are low maintenance and energy efficient. Unlike other transportation methods — such as belt conveyors — pneumatic conveyors have fewer parts and require far less maintenance so they can operate continuously for extended periods. Additionally, they consume less energy, making them environmentally friendly and cost-effective.
Factors to Consider when Choosing a Pneumatic Conveying System
Material Properties
Understanding the properties of the bulk ingredients is fundamental to pneumatic conveyor design. Factors such as particle size, density, abrasiveness, and fragility dictate the pneumatic conveying method and the convey rates that best suit the materials. For example, dilute phase might be suitable for free-flowing granules, while dense phase could be optimal for fragile powders or semi-finished mixtures of ingredients.
Throughput and Distance
The desired throughput capacity and the distance the material needs to travel play a pivotal role in the selection of the optimal pneumatic conveying system. Distance traveled includes both the horizontal and vertical distances traveled. Likewise, an excessive number of elbows or very long vertical distances will negatively impact pneumatic conveying efficiency. Dilute phase is known for high throughput and long-distance conveyance, while dense phase excels in gentle transport over shorter distances.
Material Degradation and Contamination
For sensitive materials, the risk of degradation during transport is critical. Systems like dense phase and pressure conveying offer gentler handling, minimizing these risks. The closed design of the conveying system inherently minimizes contamination risk. However, the presence of allergens or similar materials should be carefully considered when designing conveying systems.
Energy Efficiency
Energy consumption of the pneumatic conveying system is directly associated with the amount of air used to convey ingredients. Incorrect blower settings that use too much air can lead to material degradation or excessive equipment wear. Settings that are too low will cause the system to run too long to deliver the required demand. Likewise, clogged filters will lead to excessive convey time, increasing both operating costs and the risk of fugitive dust. Optimal operation requires a balanced system which will needs regular maintenance to ensure consistent performance. Systems with lower air requirements and efficient power usage help to ensure efficient operation, significantly reducing operational costs.
Maintenance and Cleanability
Easy maintenance and cleanability are vital for consistent performance of pneumatic conveying. Filter maintenance is especially important. Pneumatic conveyors have minimal moving parts, but regular maintenance is needed for all the interconnected and related equipment. Easy access points simplify upkeep and cleaning procedures.
Flexibility and Adaptability
A pneumatic conveyor’s ability to adapt to changing production demands is critical for long term efficiency. Opting for a system that can readily accommodate different materials and production variations ensures long-term viability. This is especially important as new processing lines or larger batch sizes are considered when increasing production.
Budget and Cost Analysis
Balancing performance with costs is key to prudent pneumatic conveying investments. Investment cost for automated pneumatic conveying is higher than manual material movement options, however, operating costs are much lower. This is especially true in production facilities with multiple production lines or a high-throughput production line. Investing in a system that offers optimal performance without overshooting the budget is crucial.
Questions About Pneumatic Conveying System Design?
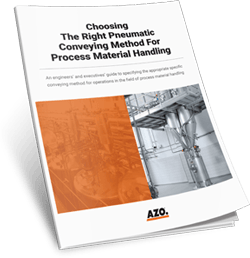
AZO’s Pneumatic Conveying Systems
AZO designs and engineers many different types of pneumatic conveying systems for bulk ingredient handling, each uniquely designed for specific projects. Depending on the required materials and the distances from storage to production, AZO will custom design the best possible pneumatic conveying solution. Each AZO pneumatic conveying system optimizes efficiency while minimizing contamination risk and ensuring material integrity throughout transfer. AZO’s product lines include:
Dilute Phase Pneumatic Conveying
Utilizing high-velocity air streams, AZO’s dilute phase pneumatic conveyors suspend and propel materials through transfer system pipes. Highly efficient in conveying large quantities of materials over considerable distances, these systems are ideal for high throughput operations in just about any industry.
Dense Phase Pneumatic Conveying
Creating gentler material transport are AZO’s dense phase pneumatic conveyors, which utilize a lower air-to-material ratio. This technique is optimal for operations handling fragile or abrasive materials or that require minimal degradation. These pneumatic conveyors are an ideal choice for handling pharmaceutical ingredients, chemicals, or fragile food inclusions or additions.
Semi-Dense Phase Pneumatic Conveying
As its name implies, this AZO system conveys materials in an operating range between dense and dilute phases. It offers a middle ground when neither dense nor dilute phase conveying is appropriate. AZO’s years of pneumatic conveying experience ensures each customer receives the optimal pneumatic conveying system for their specific production needs, ensuring high quality and cost-efficient production.
Trust AZO for Your Pneumatic Conveying System Needs
As an optimal solution for operations that must comply with stringent quality standards and regulations, AZO’s advanced pneumatic conveying solutions are ideal for food, pharmaceutical, plastics, and chemical processing industries. Every AZO pneumatic conveying system is tailored to match the unique ingredient characteristics and production demands of a given application. Their innovative solutions ensure that materials are conveyed efficiently, maintaining their purity and consistency throughout the journey from delivery to storage to production.
By investing in a robust pneumatic conveying system from AZO, manufacturers can maintain their commitment to delivering high quality products while adhering to industry standards and regulations.
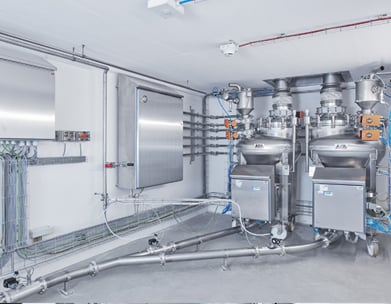
Resources About Pnuematic Conveying
Pneumatic Conveying
Streamlining Safety and Efficiency: AZO's Solution for a Candy Bar Manufacturer
The implementation of AZO's solution brought about numerous benefits. The candy bar manufacturer now had a state-of-the-art system that was perfectly sized for their production needs. This resulted in better system performance, reduced energy consumption, and a more efficient conveying path.
Solutions
Pneumatic Conveying Capabilities
Pneumatic Conveying Systems by AZO provide an ideal way for manufacturers to link stages in the process without any risk of damaging sensitive products. Perfect for granular, powdered and sensitive bulk materials, a solution can be tailored to any system parameters.
Solutions
Choosing the Right Pneumatic Conveying Method For Process Material Handling
An engineers’ and executives’ guide to specifying the appropriate specific conveying method for operations in the field of process material handling.