Bulk Bag Conditioning
Introduction
Measures taken to improve material flow of powdered or granular ingredients from bulk storage into a pneumatic conveying system are known as material conditioning. If material is clumping together or has poor flow characteristics, there are multiple ways to address these issues. Some are manual but can be time-consuming and labor intensive. Others include features built into the equipment to exponentially enhance material flow.
Bulk bag conditioning is a crucial process in bulk material handling that offers several benefits across multiple applications. It ensures the efficient and effective discharge of bulk ingredients from bags or storage bins by breaking up any clumps or compacted material. This results in improved flow and reduced downtime during the material handling process.
Additionally, bulk bag conditioning maximizes product availability by loosening and redistributing settled material or facilitating mass flow from of a bin. This reduces waste and increases productivity. Conditioning techniques are widely used in food processing, pharmaceuticals, and chemical applications where the efficient handling and discharge of bulk ingredients are essential for smooth operations. Ultimately, bulk bag conditioning plays a vital role in enhancing material flow, reducing waste, and limiting downtime in various material handling processes.
Benefits of Bulk Bag Conditioning
Improved Flow and Discharge of Bulk Ingredients and Materials
Bulk bag conditioning is ideal for materials that tend to become compacted during storage or transportation, inhibiting the free flow of powders, granules, and other ingredients handled in bulk. By breaking up the compacted material, bulk bag conditioning helps to increase the flowability of the material, creating more efficient and consistent discharge. By ensuring a smooth and uninterrupted flow of bulk ingredients during processing or transfer operations, conditioning saves time. It also reduces the need for workers to clear the clogged material manually.
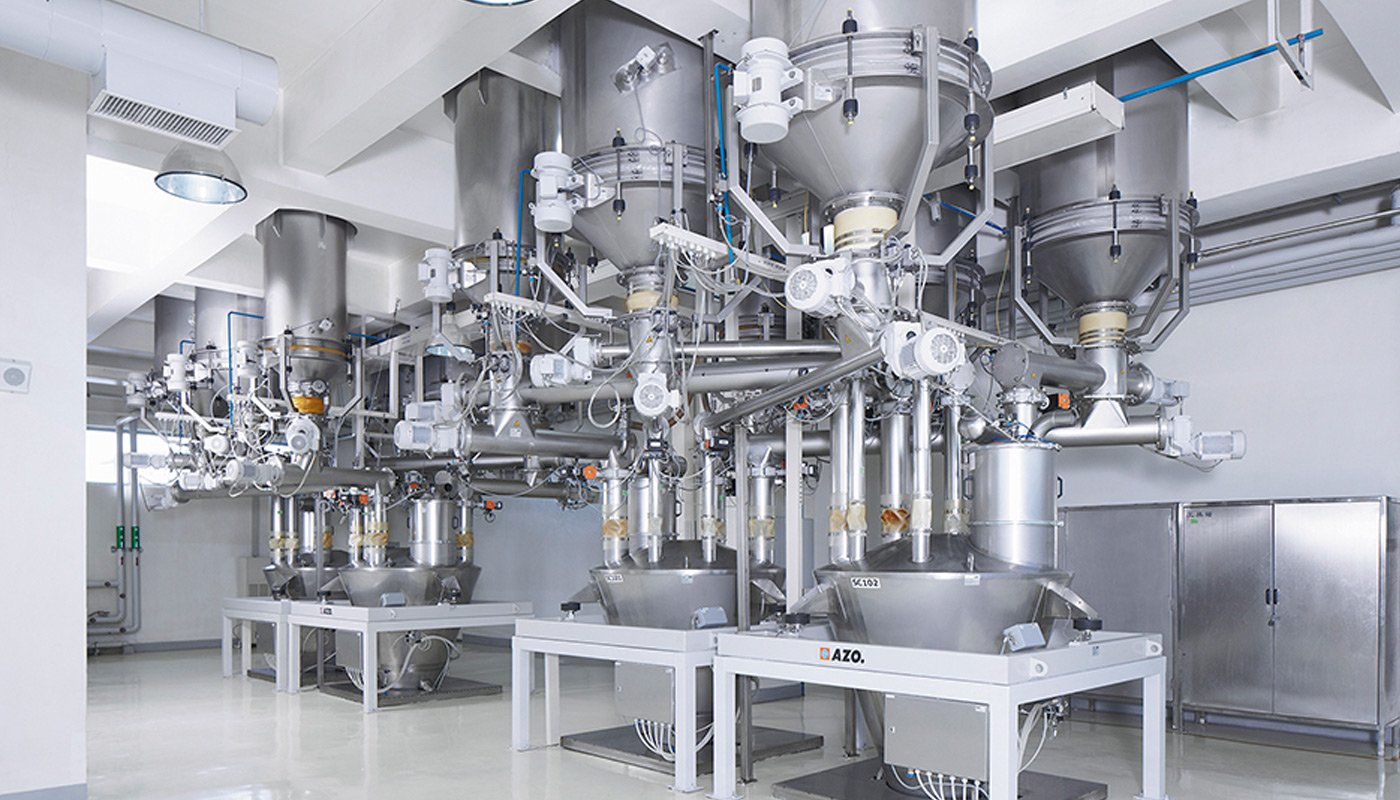
Prevention of Material Compaction and Bridging
When bulk materials are stored or transported in bulk bags, they tend to settle and become compacted over time. This leads to difficulties in flow and handling when unloading the bag. Bulk bag conditioning utilizes specialized equipment to gently massage or vibrate the bags, loosening the contents and breaking up any compacted material. The conditioning process restores the material to its original state, ensuring consistent flow. It also prevents the formation of bridges, where the material solidifies and forms a blockage inside the bag or bin. By effectively conditioning bulk bags, material compaction and bridging are minimized, generating smoother handling, improved productivity, and reduced downtime.
Reduction of Waste and Product Loss
Effectively conditioning bulk bags significantly reduces waste and product loss. This is because compacted materials often cannot be emptied out of the bulk bag, rendering the contents unusable. However, properly conditioning bulk bags minimizes the risk of blockages. This ensures the entire bag of ingredients flow smoothly and evenly to production. By enabling complete discharging, the complete contents of the bag can be utilized.
Questions About Bulk Bag Conditioning?
Factors to Consider when Choosing Bulk Bag Conditioning Solutions
Capacity and Size Requirements
When considering bulk bag conditioning for bulk ingredients, the capacity and size requirements of the bag and the unloader play a crucial role in ensuring efficient and effective operations. It is essential to accurately determine the discharge equipment’s capacity to properly match it to the size of the load and the weight of the bulk bags being handled. Overloading the conditioning system can cause equipment damage or incomplete unloading of the bulk bag. Further, it is important to consider the extra space required for the conditioning equipment to be sure the bulk bag unloader fits in the available space.
Material Compatibility and Construction
Material compatibility and construction are crucial factors to consider when implementing bulk bag conditioning. To withstand the demands of heavy-duty industrial operations, the bulk bag conditioning system’s construction must be robust and durable. Select equipment manufactured from high-quality materials that can withstand the dynamic weight and force of bulk bags, as well as the normal wear and tear of physically conditioning the bulk bag contents. A well-constructed conditioning system will ensure operator safety and efficient material handling, minimizing downtime and maintenance costs.
Additionally, the bulk bag’s fabric construction should be robust and durable enough to withstand the conditioning process, which typically involves mechanical agitation or vibration of both the bag and its contents. Reinforced seams, strong handles, and tear-resistant fabric are essential features to ensure the bags can withstand the rigorous conditioning process without compromising their integrity, which usually results in a large pile of spilled material.
Safety Features and Compliance Standards
Safety features such as interlock systems, emergency stop buttons, and guarding mechanisms are essential to prevent accidents and injuries to operators when both handling and conditioning the bulk bag. Compliance with bulk bag standards set by regulatory bodies and industry organizations is crucial to ensure that the equipment meets specific requirements for quality, safety, and performance. Adhering to these standards not only helps maintain a safe working environment but also ensures that the conditioning process is efficient and effective, minimizing the risk of contamination or loss of bulk ingredients.
Ease of Use and Maintenance
Ease of use and maintenance are crucial factors to consider when designing bulk bag conditioning systems for bulk ingredients. It is essential to choose a system that is user-friendly, allowing operators to easily load and operate the equipment. Additionally, the maintenance requirements of the system should be minimal, with easy access to critical components for cleaning and routine service. A well-designed and user-friendly bulk bag conditioning system can greatly enhance productivity and efficiency in handling bulk ingredients, reducing downtime and labor costs.
Integration with Existing Equipment
When considering bulk bag conditioning for bulk ingredients, integration with existing equipment is essential. This includes evaluating the compatibility of the conditioning system with the current material handling equipment — such as unloaders, conveyors, hoppers, or silos — to ensure seamless operation. Proper integration allows for efficient transfer of the conditioned material, avoids bottlenecks, and minimizes downtime, resulting in a continuous and reliable production process.
AZO’s Bulk Bag Conditioning Solution
When installing and maintaining bulk bag conditioning systems, there are several best practices to keep in mind. AZO installations typically place the bulk bag conditioner in the unloader so as to not hinder the normal transfer and unloading of bulk bags. AZO Bulk Bag Conditioning Systems are equipped with features such as massage paddles or agitators. These components help break up and loosen compacted materials inside the bags after the bulk bag has been positioned for unloading.
In terms of maintenance, AZO Bulk Bag Conditioning Solutions are designed to support easy inspections and cleaning of the equipment. Essential to ensure optimal performance, AZO systems are highly accessible to enable routine checks for any signs of wear or damage. Maintenance also ensures that the conditioning equipment allows the bag to be completely emptied after each use. Additionally, it is important to follow AZO’s guidelines for routine maintenance tasks — such as lubrication or hydraulic or pneumatic connections — to prolong the useful life of the equipment.
Trust AZO for Your Bulk Bag Conditioning Needs
Bulk bag conditioning offers numerous benefits and is an important part of production processes that utilize any material that is not free flowing or tends to settle and clump. It ensures the proper flow and discharge of bulk materials by eliminating issues such as bridging, clumping, and compacting. AZO’s Bulk Bag Conditioning Systems effectively loosen and break up compacted materials to improve productivity, reduce downtime, and minimize the risk of equipment damage.
By investing in a bulk bag conditioning system from AZO, manufacturers can optimize their bulk material handling processes, increase operational efficiency, and ultimately reduce costs.
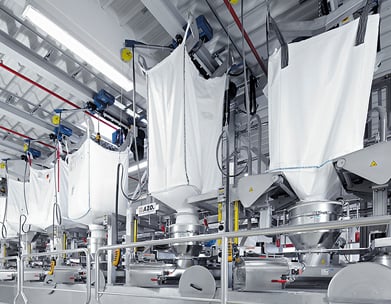
Resources About Bulk Bag Conditioning
Reliable conveying
Case Study Headline Here Lorem Isum Dolor Caseum Elefiend
Sed laoreet non arcu a facilisis. Nunc a nisi ex. Sed eleifend tellus sit amet magna malesuada, nec dignissim. Sed laoreet non arcu a facilisis. amet.
Bulk Materials
Case Study Headline Here Lorem Isum Dolor Caseum Elefiend
Sed laoreet non arcu a facilisis. Nunc a nisi ex. Sed eleifend tellus sit amet magna malesuada, nec dignissim. Sed laoreet non arcu a facilisis. amet.
Reliable conveying
Case Study Headline Here Lorem Isum Dolor Caseum Elefiend
Sed laoreet non arcu a facilisis. Nunc a nisi ex. Sed eleifend tellus sit amet magna malesuada, nec dignissim. Sed laoreet non arcu a facilisis. amet.