AZO’s heavy-duty super sack unloader — or bulk bag unloader, as it’s also called — is designed to unload and discharge any and all materials from bulk bags.
Bulk Handling in the Personal Care Products Industry
Let AZO engineer a bulk handling system that dispenses personal care product ingredients with a high degree of accuracy, minimizes waste, and prevents contamination.
Bulk Ingredient Handling for the Personal Care Products Industry: Overview
Personal care product manufacturers handle a broad range of expensive bulk dry ingredients — including TiO2, fumed silica, and super absorbent polymers — to create the necessities consumers rely on daily. Minimizing waste, ensuring accurate handling, and safeguarding product integrity are key concerns. Whether you’re manufacturing toothpaste, lotion, eyeliner, hand soap, or other personal care products, you can trust AZO’s decades of experience designing, engineering, and supporting safe and reliable bulk material handling systems in manufacturing operations where product purity is essential.
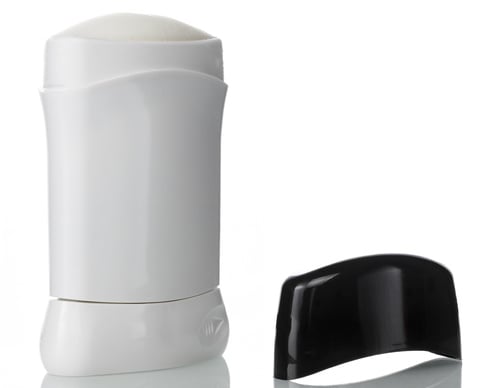
Typical Personal Products Industry System
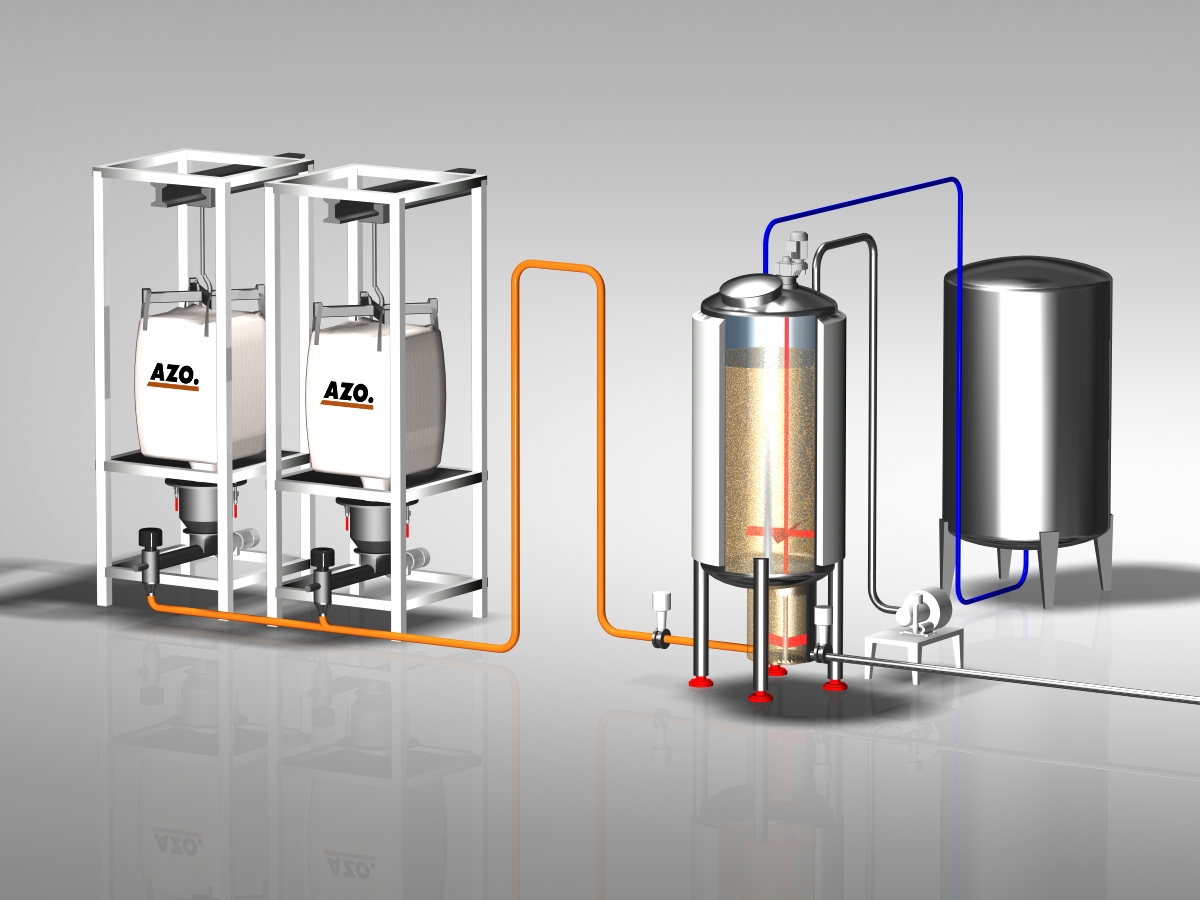
BBA (Bulk Bag Docking Device)
The AZO docking system allows for easy handling while preventing contamination to the environment.
DFS (Dosing Feed Screw)
The AZO DFS dosing screw allows for the continuous and discontinuous conveying and metering of bulk materials in conveying lines, scales, and more.
Solid (Powder) Product Convey Line
AZO designs and engineers many different types of pneumatic conveying systems for bulk ingredient handling, each uniquely designed for specific projects.
Liquid Mixing Tank (Buyout Equipment)
Liquid Ingredient (Water) Convey Line
Each AZO pneumatic conveying system optimizes efficiency while minimizing contamination risk and ensuring material integrity throughout transfer.
Liquid Ring Pump (Buyout Equipment)
Liquid Mixed Product Convey Line
AZO’s years of pneumatic conveying experience ensures each customer receives the optimal pneumatic conveying system for their specific production needs.
Liquid Storage Tank (Buyout Equipment)
For liquid and viscous materials, AZO offers tanks in various shapes and sizes, each equipped with features to ensure exacting storage and controlled processing.
Bulk Ingredient Handling for the Personal Care Products Industry: Common Challenges

Accurate weighing of minor and micro ingredients.

Accurate weighing of minor and micro ingredients.
Personal care products incorporate a wide variety of ingredients, often in small amounts. Accuracy is of paramount importance when weighing micro and minor ingredients, which can be extremely expensive or stored and dispensed in small quantities. To reduce waste, ingredient handling systems must be designed to deal with each unique ingredient properly.

Handling non-free flowing ingredients.

Handling non-free flowing ingredients.
Handling non-free flowing personal care product ingredients can be exceptionally difficult, with each presenting a unique challenge. It is important to perform lab testing of non-free flowing ingredients to verify proper design parameters. These parameters must be considered when designing material storage, conditioning, weighing, dosing, and dispensing for difficult-to-handle ingredients.

Personal care product manufacturers must meet hygiene and consumer safety requirements.

Personal care product manufacturers must meet hygiene and consumer safety requirements.
Ingredient integrity and safety is a critical concern for personal care product manufacturers, as contamination can not only affect end product quality, but also pose risks to consumers. Whether dosing or weighing, personal care product manufacturers must comply with proper hygienic handling practices for all bulk ingredients through regular sanitation and wash-downs. They must also eliminate cross-contamination risks, verify cleanliness, and prevent ingredient cross-contact.

Personal care product manufacturers must contain dust.

Personal care product manufacturers must contain dust.
A method for containing the high volumes of dust generated by many bulk ingredients used in personal care product manufacturing should be included in every bulk material handling system design. Fugitive dust can lead to any number of problems, including attracting vermin, operator exposure, or in the worst case, combustion. Improper dust control creates an unsafe working environment for personnel and increases the risk of product contamination.

Proper storage and isolation of bulk ingredients.

Proper storage and isolation of bulk ingredients.
Individually storing and isolating bulk ingredients from one another is a critical challenge. Many personal care product manufacturers must handle different ingredients with different characteristics and significantly different amounts. The unique qualities of each ingredient and the amount required in each recipe must be considered when selecting bulk storage and handling equipment.

Government regulation and accurate lot tracking.

Government regulation and accurate lot tracking.
Government requirements for safe handling and personal care product manufacturing include mandates for accurate tracking of every ingredient used in each batch. Compliance failures such as inaccurate batching or documentation errors — mistakes that commonly occur in manual handling applications — significantly increase the risk of fines or quality issues.
Bulk Ingredients for the Personal Products Industry
-
TiO2
TiO2
TiO2
Bright white and used in a variety of everyday products, TiO2 is an extremely common ingredient in many bulk ingredient handling operations, including personal products, poly and plastics, chemicals, and pharmaceuticals. Characterized by fine particles that flow poorly, TiO2 is moderately abrasive and forms heavy, dense clumps. These critical attributes can make emptying this ingredient out of storage vessels or successfully conveying it challenging. AZO’s engineering team carefully considers each of these factors to ensure the design of a TiO2 handling system is safe, reliable, and dust free.
-
Fumed Silica
Fumed Silica
Fumed Silica
Composed of very fine, non-porous particles of silicon dioxide (SiO2), fumed silica powder has a high surface area and light density. Due to its extremely high surface area, it is an effective thickening and reinforcing agent in many products. Whether it’s used in personal products, poly and plastics processing, or chemicals, fumed silica’s unique characteristics require special material handling solutions. It is prone to producing high amounts of dust, which is easily combustible and a personnel risk. AZO’s engineering team carefully considers each of these factors to design a bulk fumed silica material handling system that ensures safe, reliable flow.
-
Diatomaceous Earth
Diatomaceous Earth
Diatomaceous Earth
A type of crystalline silica made from pulverized sedimentary rock, diatomaceous earth comes in many forms, including pellets, particles, or powder. In its powdered form, this naturally occurring ingredient has a high surface area and light density. It is an ingredient used in a range of beverage and food grade filtration applications and in many industrial applications. Whether it’s used in manufacturing of personal products, pharmaceuticals, chemicals, or beverage filtration, diatomaceous earth powder’s unique characteristics require special material handling solutions. It is prone to producing high amounts of dust, which is a carcinogen. AZO’s engineering team carefully considers each of these factors to ensure the design of a diatomaceous earth handling system is safe, reliable, and dust free.
TiO2
Bright white and used in a variety of everyday products, TiO2 is an extremely common ingredient in many bulk ingredient handling operations, including personal products, poly and plastics, chemicals, and pharmaceuticals. Characterized by fine particles that flow poorly, TiO2 is moderately abrasive and forms heavy, dense clumps. These critical attributes can make emptying this ingredient out of storage vessels or successfully conveying it challenging. AZO’s engineering team carefully considers each of these factors to ensure the design of a TiO2 handling system is safe, reliable, and dust free.
Fumed Silica
Composed of very fine, non-porous particles of silicon dioxide (SiO2), fumed silica powder has a high surface area and light density. Due to its extremely high surface area, it is an effective thickening and reinforcing agent in many products. Whether it’s used in personal products, poly and plastics processing, or chemicals, fumed silica’s unique characteristics require special material handling solutions. It is prone to producing high amounts of dust, which is easily combustible and a personnel risk. AZO’s engineering team carefully considers each of these factors to design a bulk fumed silica material handling system that ensures safe, reliable flow.
Diatomaceous Earth
A type of crystalline silica made from pulverized sedimentary rock, diatomaceous earth comes in many forms, including pellets, particles, or powder. In its powdered form, this naturally occurring ingredient has a high surface area and light density. It is an ingredient used in a range of beverage and food grade filtration applications and in many industrial applications. Whether it’s used in manufacturing of personal products, pharmaceuticals, chemicals, or beverage filtration, diatomaceous earth powder’s unique characteristics require special material handling solutions. It is prone to producing high amounts of dust, which is a carcinogen. AZO’s engineering team carefully considers each of these factors to ensure the design of a diatomaceous earth handling system is safe, reliable, and dust free.
AZO’s Bulk Ingredient Handling Solutions for the Personal Care Products Industry: Outcomes & Benefits
AZO’s experienced design engineers understand the unique challenges facing manufacturers of the personal care products. Every bulk ingredient handling system we create incorporates equipment and solutions that reliably and effectively address the challenges outlined above. As a single-source provider of automated ingredient system equipment, AZO designs and engineers bulk handling solutions that enhance both safety and productivity in your facility.
With an AZO bulk ingredient handling system, your personal care products manufacturing operation will:
- Ensure product consistency and quality via highly accurate automatic weighing and dosing of bulk, minor, and micro ingredients.
- Maintain proper hygiene and eliminate cross-contamination risks with easy-to-clean equipment.
- Easily accommodate a broad range of personal care product formulations and ingredients.
- Keep employees safe by reducing ergonomic injuries and accidents.
- Consistently and accurately comply with government track-and-trace requirements.
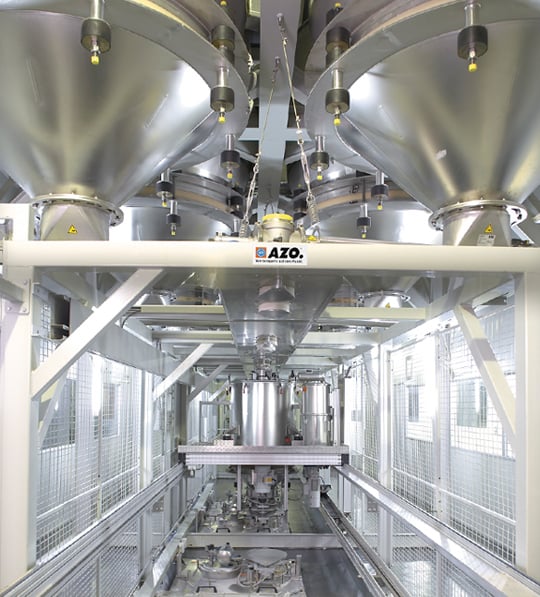
AZO’s Bulk Ingredient Handling Systems for the Personal Care Products Industry: Equipment & Engineering Solutions
AZO backs the personal care products industry with comprehensive, engineering-centric design and support. Your solution will match your unique requirements and optimized for the safest, most reliable handling process. AZO automated systems for personal care products manufacturing plants typically include: