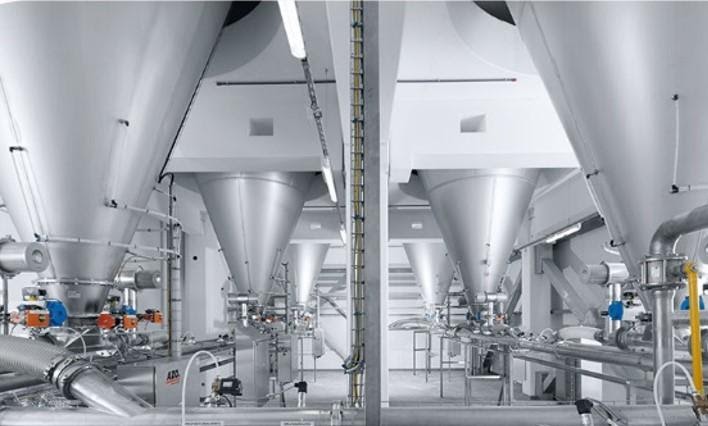
When companies experience issues related to the flow of their materials, it is important to ask some critical questions. These can include “Is the problem area accessible?” “Does the problem area include a scale or a moving piece of equipment?” and “What is the cost to install and operate a flow aid to assist this problem?”
Manufacturers might be surprised to learn that it can be easier and cheaper to install these types of aids upon system setup, but some more generalized questions can give manufacturers more of a basic understanding of why these problems arise in the first place. This understanding can help a manufacturer choose the appropriate flow aid and avoid costly holdups in the future. What follows are three questions whose answers explain how the concepts “mass flow,” “funnel flow” and “FIFO” dictate how materials can be most efficiently (and safely) handled:
What is the difference between ‘mass flow’ and ‘funnel flow’?
“Mass flow” and “funnel flow” are essentially the two traditional pillars that explain how material flows out of a vessel. Mass flow bin is where all the materials move from the top of the vessel to the bottom in an even fashion. Funnel flow is represented when material starts to discharge from the center of the vessel and what is known as “slower-moving region” to the outside of stored mass. Further, it is also possible to achieve (in some situations) where stagnate material is left behind.
Essentially, mass flow takes place when all material in a vessel is in motion during the discharge of the vessel outlet. All moved material flows in a downward motion en masse. This avoids funnel flow, bridging, arching and stagnant regions.
What is “FIFO” capability?
While, in general, many vessels are designed to promote mass flow, it isn't necessarily the end goal of every application. This is because there are multiple factors that play into whether mass flow is actually achievable.
Regardless of the situation, one of the most important ideas within the subject of storage geometry is “FIFO,” or “first-in, first-out,” capability. Particularly in food applications, manufacturers must ensure that ingredients with a shelf life are being consumed in an orderly fashion. FIFO makes sure that there isn't that stagnating material to persist inside of a vessel beyond its identified shelf life. FIFO capability means that the material is being removed from the vessel in the same order that it was put into it. What was “first-in,” is also “first” of what comes “out” of the storage vessel.
Another concern besides storage life is that the material might become less “potent” over time. FIFO and mass flow would ensure that said ingredient doesn’t degrade before it reaches its end goal in a process. Still, there are times where equipment manufacturers use discharge aids to promote FIFO while not necessarily achieving true mass flow. Even if true mass flow cannot be achieved due to physical limitations, discharge aids can guide the process toward achieving FIFO in the end.
How does non-flowing material pose safety concerns?
Stagnant material should be prevented for a variety of reasons, but additionally, there are potential safety hazards from material becoming hung up in a vessel. If product is “bridged” in a silo (and the bridge collapses), the material can free-fall with enough force to damage equipment. Even worse, this situation can cause serious harm to operators. If a bridge collapses (and material drops rapidly and forcefully into the internal void space below), oil-canning or imploding can also become a concern. This can cause permanent deformation of a storage silo.
If product is consistently flowing in a way that is expected, then there are less unpredictable scenarios in which a potential catastrophic failure of the equipment and worker safety is jeopardized. Gravity is always in effect. Any type of material will reach a tipping point and cause an avalanche to occur within a storage vessel. By using flow aids like fluidization or a live-action vibration bottom, manufacturers can greatly reduce the risk of potentially dangerous erratic flow conditions.
A new, free guide from AZO further elaborates on various mechanical devices that are used to apply energy into material in order to induce flow. “Flow and Functionality: Determining The Proper Discharge Aids For Your Bulk Material Handling Process” contains pertinent information about many machines that are often used in concert with each other (as well as flow agents) to overcome the friction between material and the wall of storage vessels.
If you find that you have any other conveying queries, you can always feel free to speak to an AZO specialist. We have more than seven decades of experience in handling raw materials and shaping ingredient automation along the way. Contact our sales team for any questions on how to help your plant and processes run smoothly.