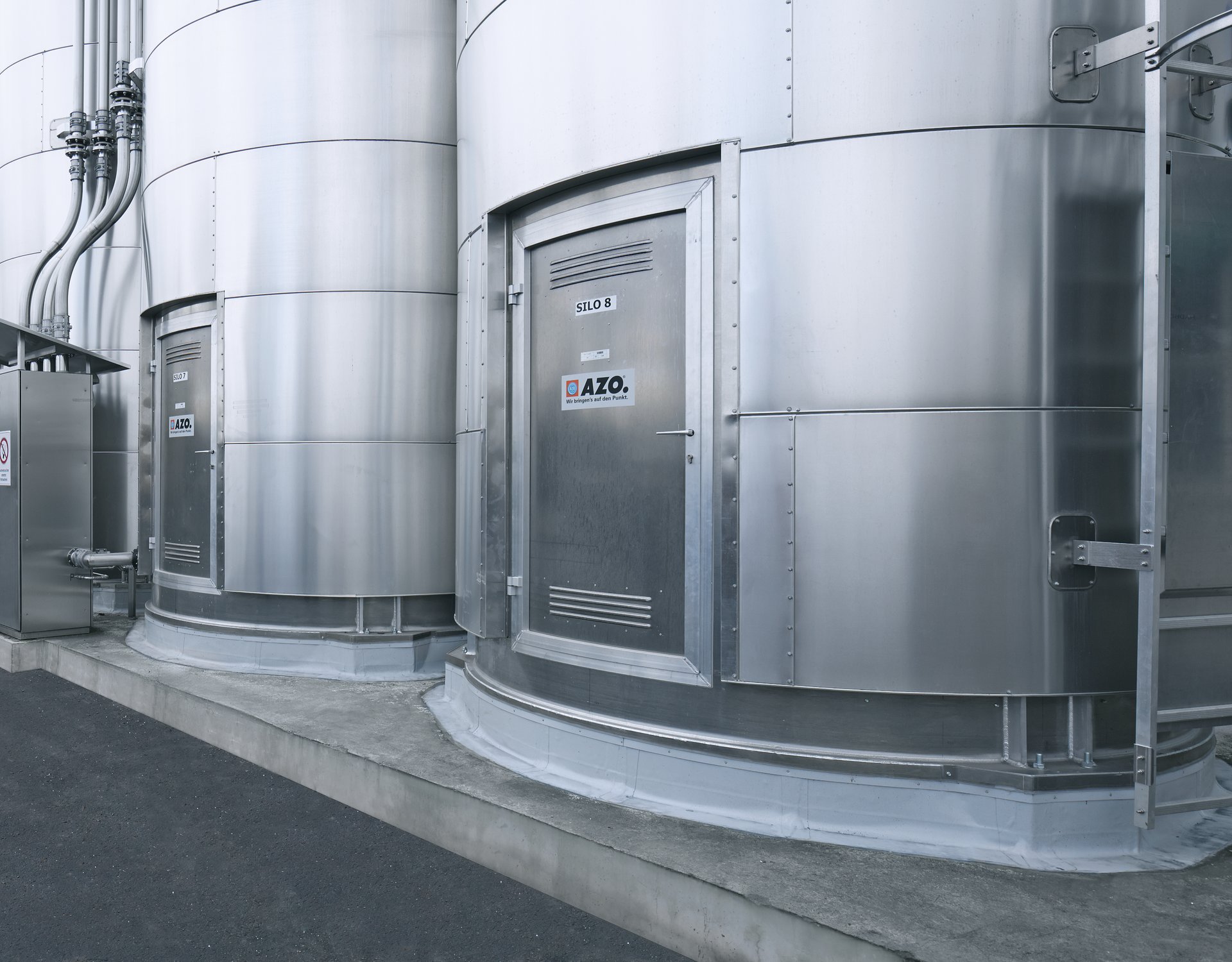
When Engineering, Procurement, and Construction (EPC) contractors take on multi-million dollar projects, they’re managing dozens of vendors and systems all at once. Bulk material handling might seem like a small piece of the puzzle, but it can become a major source of risk if not handled correctly.
Powder flow issues, hygienic design, and explosion hazards don’t just threaten compliance. They jeopardize the entire plant’s safety, throughput, and long-term efficiency. Construction firms excel at building big, and they need strong partners who know the nuances of dry bulk material behavior and dust explosion mitigation.
That’s where AZO steps in. We’re often brought on as the specialty partner for ingredient systems, whether it’s a green field project or built-to-suit. Our job is to make sure the right materials get to the right place, in the right condition, without causing issues. When done well, our role goes largely unnoticed and that’s by design. We help everything else work as intended.
When Bulk Ingredient Handling Goes Wrong in EPC Builds
Even for the most well-orchestrated EPC projects, ingredient handling systems can become a source of delays, compliance issues, or costly rework if not addressed early and holistically. The most common challenges we see across the food processing industry, beverages, pharmaceutical, and chemical manufacturing fall into five core categories:
1. Combustible Dust and Explosion Hazards
Many bulk dry materials — like starches, flours, and fine powders — are classified as combustible. When systems aren't properly grounded, vented, or designed for dust containment, the result can be unsafe conditions and failed inspections. To meet this challenge, follow all NFPA standards, perform upfront DHAs (Dust Hazard Analyses), and opt for ATEX-compliant equipment with built-in explosion protection features to prevent these risks from snowballing.2. Material Flow Blockages
Poor material flow and blockages disrupts production, causing downtime, delays, and inefficiencies — even increased maintenance costs. Solve this by selecting the right pneumatic conveying systems with technology such as air sweeps, de-lumpers, screw feeders, and condition-based flow control that are backed by lab-tested data to ensure each ingredient behaves as expected in the system.3. Allergen Control
In food industry and pharmaceutical builds, contamination isn’t just a quality issue; it’s a regulatory one. Prioritize systems with smooth, cleanable surfaces, isolation valves, and hygienic connections that reduce allergen crossover and simplify cleaning. Allergen isolation technologies such as fully enclosed systems can also minimize cross-contamination exposure. Bulk ingredient storage solutions and bulk bag unloaders can make a big difference here.4. Ingredient Dosing Errors
Even small inaccuracies in weighing or dosing can ruin a batch. This is a huge problem in pharmaceutical and food production, where precise formulation of micro and minor ingredients safeguards human health. Systems must be engineered for recipe-level precision and include automatic recalibration features for consistency in high-throughput environments with dozens or hundreds of formulas.5. Equipment Leaks and Poor Seals
Leaks aren’t just messy — they waste material and compromise the production area. From day one, equipment should be built with industrial-grade sealing and leak prevention to minimize ingredient loss and dust escape. This also helps ensure regulatory compliance.
Overcoming Bulk Material Handling Challenges With AZO
When AZO partners with an EPC, we solve these challenges with our specialized equipment. But before we even talk tech, we start with full-system engineering and layout.
No matter your level of ingredient handling knowledge, we’ll take your Request for Proposal and give you a Value Engineering Package that includes the best system design for your client. During the development stage, we create custom ingredient handling solutions with quotes.
Adopting your EPC’s project execution methodology, our project and sales managers will coordinate across your departments. That may include working with business unit managers and BDRs, process engineers, system integrators, and procurement to take the project from development through execution.
Before anything is installed, we test material behavior in-house and provide performance guarantees for flow rates, dust control, and more. Finally, we offer ongoing support through Site Acceptance Testing (SAT) and start-up so your bulk material handling equipment functions as promised.
Here’s what we need from you to get started on your project:
- Complete ingredient list
- Material characteristics
- Building layout
- Process narrative
- Production performance requirements and criteria
Want to see this process in action? Here’s a case study of one of our high-volume projects.
How AZO Partnered With an EPC to Scale Pet Food Production
The Challenge:
A major pet food company needed a brand-new, multi-million dollar facility to produce pet food for cats and dogs — specifically to support growing demand. They turned to AZO to engineer the dry bulk ingredient handling system at the front end of the process. The solution required storage and precise batching of 24 bulk dry ingredients, including whole corn and rice that had to be milled, mixed, and transferred to downstream mixers.
Design, Coordination & Delivery:
We joined the project early, collaborating with engineering teams and vendors to align process design, layout, and timeline. With just nine months from purchase order to on-site delivery, timing was critical. Silos had to be installed before the building’s walls and roof were enclosed.
We followed the DHA for ingredients identified as combustible dust, and performed extensive lab testing to confirm flow rates, grain sizing, and mix homogeneity to guarantee performance handling for 200 recipe variations.
On site, screeners were installed at ingredient intake and after milling/final mixing to ensure quality assurance and process control, and prevent foreign objects (a choke hazard for pets) from ending up in finished food.
The Results:
AZO delivered a robust, integrated solution that met NFPA standards featuring bulk silos, hammer mills, dosing screws, pneumatic conveying, vacuum scale receivers, screeners, and magnets. The system consistently achieved 4 batches per hour per mixer for 8 total batches per hour throughput. This means one batch every 15 minutes. Delivered on time and on budget, our solution helped the EPC’s pet food client deliver on product quality and expand their business.
Why Big EPC Projects Need AZO-Level Support
In large-scale builds, the smallest systems can create the biggest problems if overlooked. Ingredient handling is one of those systems — quiet, but critical. It impacts everything from safety and sanitation to throughput and product consistency. That’s why the most successful EPC contractors bring in AZO early in the development process.
We thrive in high-stakes, high-standards environments. Our solutions can scale and adapt to your project's unique requirements and budget. Whether it's ensuring NFPA compliance, eliminating material flow issues, or achieving batch-to-batch dosing accuracy, AZO designs with the full lifecycle of the plant in mind. We understand how upstream decisions impact downstream processes like blending, conveying, packaging, and quality control.
When you work with AZO, you're not just getting equipment — you’re getting a long-term partner who anticipates issues before they happen. We align with your workflow, deliver performance you can count on, and stick with you through start-up and beyond. Our end goal is to give you peace of mind with your bulk material handling, knowing you can depend upon us when projects get tough.
Need some support with your bulk ingredient handling system?
We'll help design a solution that integrates smoothly with your schedule and performs long after the ribbon is cut. Contact us to get started.