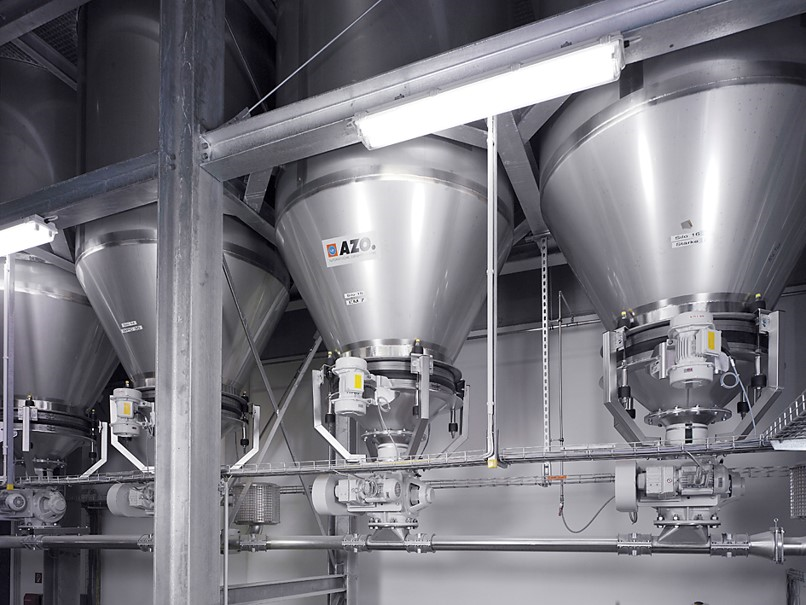
Depending on the materials you and your operation are looking to convey, dilute phase and dense phase conveying will better fit different scenarios.
A pickup point in a dilute phase vacuum pneumatic conveying system
Whether or not material should be conveyed gently, ingredients should be protected against segregation (de-mixing) or if the effects of abrasion on your equipment should be minimized will determine which type of conveying is appropriate for your process. The particle size of your material and other key characteristics also play critical roles when opting for either dilute or dense phase conveying.
As you can greatly optimize your conveying rate by optimizing your flow and velocity, we’ll take a look at the benefits to each method as well as some other key factors in this post.
Friable and abrasive materials benefit from dense phase
In dense phase conveying, slugs of material are separated by alternating pockets of air to prevent segregation. Here’s how that translates to materials you might want to convey: Friable or abrasive products also benefit from dense phase conveying as it is gentle. Essentially the benefits of dense phase conveying include gentle, lower conveying velocity with little or no segregation.
A destination point for a dense phase vacuum conveying system
Since the conveying air velocity is much lower in a dense-phase system than a dilute phase system by comparison, particles are subjected to less degradation or segregation. The material is not moving as fast as dilute and not therefore in risk of breaking.
Dilute phase handles a wide range of product-flow characteristics
Most materials can be successfully conveyed in dilute phase systems. Dilute is essentially the default mode of conveying for most operations because it can easily adapt to materials with a wide range of product-flow characteristics (such as particle size and bulk density). This is because this mode of conveying is more forgiving and versatile.
A pickup airlock feed of a dilute phase pressure conveying system
Dilute phase conveying is also the most economical mode in many cases because the equipment used in these systems are typically easier to clean and maintain. Dense phase systems typically require higher pressures, and vessels built to withstand these pressures must meet codes set by the American Society of Mechanical Engineers (ASME). These heavy vessels are more difficult to take apart and inspect (and therefore clean) due to the amount of extra flanges, bolts and fasteners required.
In the end, dilute phase conveying is most flexible, economical and readily expandable. From granular plastic to finely divided minerals, dilute phase tends to be the most efficient way to convey materials.
The convey path determines pairings of dilute (or) dense with vacuum (or) pressure conveying
As distance is a critical factor that determines whether a vacuum or pressure system is suitable, the makeup of a material typically determines whether dense or dilute phase conveying is more appropriate.
Convey paths can often include “elbows,” which are any bends or changes in the direction of a pipe. Operations that convey abrasive materials using dilute phase either have reinforced elbows or, alternatively, specially engineered “deflector elbows.” These elbows deflect air and materials away from the corner of the elbow through their design. Abrasion-resistant or heavy wall piping will also be required in many applications.
Destination filter receivers of a dense phase pressure conveying system
If rates allow, dense phase conveying can be utilized in this scenario for an overall gentle process. Material will still abrade piping and elbows to a degree during dense phase transport because there will always be some kind of friction between the pipe wall and the product. Still, these abrasive effects are minimized in a dense phase system.
Though some operations may invest in abrasion resistant-elbows, even these become worn down and destroyed eventually. For example, conveying silica sand through a pipe will always result in some degree of abrasion.
Conveying above saltation velocity keeps particles suspended
Saltation velocity represents the point where product falls out of an airstream. Conveying above saltation velocity is an important factor as it allows particles to flow through the system with sufficient velocity to keep particles suspended.
Generally, a characteristic of dilute phase conveying is modeled by conveying in safe ranges above saltation velocity. By contrast, when conveying in dense phase, the majority of the system operates below saltation velocity.
Specifically, at AZO, there are various solutions we can provide with custom designs where dilute phase will surprisingly not cause damage to your delicate materials. Specific results can be determined through lab tests at the Thorp Callaway Ingredient Automation Test Facility located in Memphis, TN. Here at this in-house lab, AZO technicians can properly assess if material can be successfully handled in a pneumatic conveying system. The most appropriate type of conveying method for your materials can also be identified here.
Testing is especially recommended when the optimum type of conveying solution for products where degradation and or segregation is a concern. We welcome you and recommend that you witness the tests trials in person, or videos can be sent demonstrating how they’re conducted. AZO also provides vacuum-dense conveying, which many of our competitors don't offer.
If you have any other questions or concerns regarding plant process challenges, contact our sales engineers. AZO has decades of experience in the ingredient automation world and tons of topics we’ve covered on our blog. Our pneumatic conveying guide covers the unique benefits of dense, dilute, pressure and vacuum conveying as well as other topics like how to avoid breakage with “hybrid conveying” and the hidden costs related to conveying systems.