The COVID-19 pandemic exposed the vulnerabilities in companies' relentless pursuit of supply chain efficiency, resulting in production disruptions and the inability to adapt to changing markets and consumer habits. This shift from short-term issues to long-term disruptions challenged conventional management beliefs. The pandemic forced a renewed focus on risk management, as managers now recognize the need to anticipate and prepare for a range of potential disruptions beyond worker safety and packaging challenges.
Hybrid Manufacturing Operations for Flexibility and Resilience
Our new guide, “Hybrid Manufacturing Operations for Flexibility and Resilience” tackles how a “hybrid” alternative between diversification and consolidation might just better prepare a company for disruption and economic uncertainty.
In this guide, you will find:
- Advantages and disadvantages of traditional consolidate vs. diversify strategies
- Various operational and financial considerations for both strategies
- A hybrid solutions of both strategies
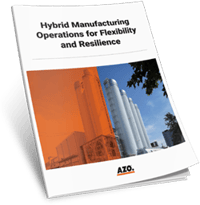
Download the Free Guide
What’s Inside?

Acknowledge the impact of COVID-19.

Acknowledge the impact of COVID-19.

Compare preparation for risk versus uncertainity.

Compare preparation for risk versus uncertainity.
Business decisions typically prioritize risk, where the probability distribution of outcomes is known and can be managed with proactive measures like insurance. In contrast, uncertainty, where both the future events and their probabilities are unknown, poses a greater challenge. Uncertainty can't be quantified as easily, making it more complex to prepare for.
Mitigating risk involves quantifiable costs, but addressing uncertainty is more challenging, as it involves scenarios that can't be reasonably anticipated. Examples of uncertainty include unexpected shifts in demand (e.g., gluten-free trends), workforce disruptions, or trade disputes disrupting supply chains. Managers often focus on risk mitigation, neglecting uncertainty due to its complexity.

Understand how many plants are needed to balance risk and cost.

Understand how many plants are needed to balance risk and cost.
Companies often use diversification of manufacturing locations to manage risk and uncertainty. The number of manufacturing plants a company needs is a fundamental question, balancing risk and cost. New plants can be created through greenfield projects, business acquisitions, or regional supply chain considerations. However, sales growth projections and optimistic momentum often drive these decisions, and the initial justifications are rarely revisited until a crisis occurs. This results in systemic risks becoming embedded in normal business operations.
Moreover, many factories remain stagnant due to a lack of capital investment, leading to inefficiency and obsolescence. Modest, continuous investments can generate significant returns in existing facilities, making them more cost-effective and less risky than optimistic greenfield investments. Unfortunately, many companies overlook these opportunities for improvement.

Assess the remaining scars from past economic shocks.

Assess the remaining scars from past economic shocks.
COVID-19 and the Russian-Ukrainian war have disrupted the global economy. COVID initially caused labor, packaging, and logistical challenges, altering consumer spending patterns. Despite adapting to living with COVID, the Russian invasion introduced new disruptions to energy and commodities markets, causing raw material shortages, inflation, and inventory gluts. These disruptions were interrelated and forced companies to be flexible and act quickly. Manufacturing challenges included labor shortages, packaging shifts, logistics disruptions, raw material shortages, inflation, and inventory imbalances. China's Zero COVID policy also impacted production and logistics. Areas prone to natural disasters and climate change-related issues pose additional risks and uncertainties for the future.

Think beyond the consolidation vs. diversification conversation.

Think beyond the consolidation vs. diversification conversation.
AZO suggests that manufacturers should view their process automation and manufacturing decisions as options to navigate periods of uncertainty. These decisions should ideally support current needs, mitigate risks, and provide a flexible framework for adapting to changing conditions. Rather than choosing between consolidation and diversification, companies can now adopt a hybrid approach, leveraging modern technology and production methods to manage complexity and build resilience into their operations.

Access a roadmap to building flexibility into your plant.

Access a roadmap to building flexibility into your plant.
The seven step process involves taking inventory of the current operation, identifying risks and market trends, researching technology, creating an ideal hybrid solution, conducting a gap analysis, and defining goals and technology requirements. This structured approach aims to enhance resilience in the face of uncertainties and ensures that capital investments are well-considered and rationally executed, enabling businesses to address potential risks more effectively.