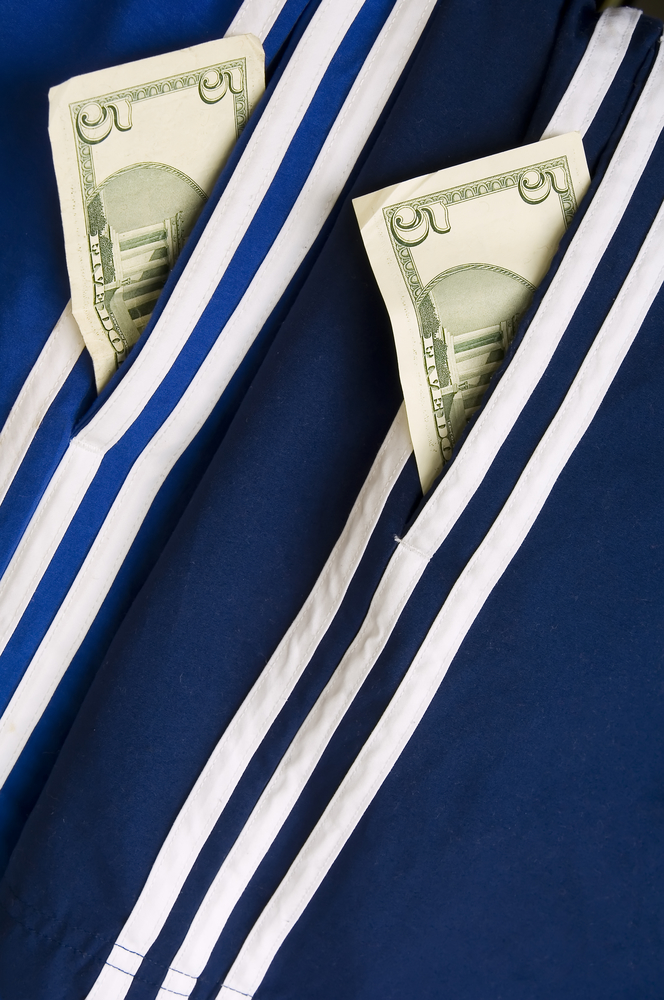
Compressed air is used in a vast majority of bulk solids handling systems to operate equipment such as valves, flow aids and bearing purges. Compressed air is used in almost all industrial facilities and a staggering number of these systems have leaks. The U.S. Department of Energy estimates an average leakage rate of 25%, up to as much as 80%. This means a significant amount of energy and money is being wasted on lost air.
Economics of Compressed Air Leaks
Pneumatic conveying systems typically use compressors as the motive air source, requiring a great amount of air flow. Leaks in these compressed air systems can result in wasted electricity, reduced performance of the overall bulk solids handling system, decreased productivity, and increased maintenance costs. Leaks can also negatively impact equipment life and overall plant productivity.
Compressed air leaks reduce the amount of air flow needed to move product due to decreased pressure at use points. To offset this loss, facilities often turn up the compressor pressure to compensate for the leakage. Of course, increased pressure will also cause more air to flow out of a leak. In other words, higher operating pressure increases the inefficiency and makes a bad problem worse.
Leaks can be Expensive
The annual energy cost for a single leak can be estimated with the following formula:
Annual Cost of Leak = Leakage Rate (Cubic Feet per Minute) x Kilowatt/CFM x Operating Hours x Cost/KH per Kilowatt Hour)
Example:
- A 1/16” leak operating at 100 PSIG will reduce compressed air flow by 6.5 CFM.
- Compressor efficiency is typically 18 kilowatt/100 cubic feet/minute, or 0.18 kW/CFM.
- Average electricity cost per kilowatt hour in late 2022 is $0.1345/kWh
- Assuming compressor operates 8,000 hours/year
Annual Cost of Leak = 6.5 CFM x 0.18 kW/CFM x $0.1345/kWh x 8,000 hours x = $1,259 loss/year for a single small leak!
Keep in mind that leaks in any compressed air system are cumulative, i.e. two 1/16” leaks would double the loss to $2,518. A poorly maintained pneumatic conveying system with multiple leaks can quickly add up to a significant operating expense. And guess what - because it still moves ingredients from storage to processing, would you know that anything needs fixing? If it’s not broken…but in a large system, leaks could easily increase operating costs over $100,000 a year!
But that’s not the end of it. Leaks can also cause system pressure to fluctuate, causing air-operated devices to not work due to a lack of air pressure or flow. This fluctuation could lead to equipment alarms or system shutdown and lost production. A leaky compressed air system may not be able to take on additional capacity when surges in production occur. Even under normal operation, leaks cause extra strain on the compressed air system as it is already running harder than normal.
Since the compressed air system is already being overworked, the air compressor will run more frequently, increasing the need to service it and ultimately reducing its service life.
In general, compressed air leaks should be searched from the air compressor to all the use points. The more connections and hoses the system contains, the more leaks are possible. Leakage points are often located in the last 30 feet of piping/hoses closest to usage point. This is where the smallest piping and hose are located, as well as the most vibration and stress from the operating equipment.
Searching for Leaks
In searching for leaks, the common problem areas include:
- Couplings, hoses, tubes and fittings. Tubes and push-to-lock fittings are common problems.
- Disconnects. O-rings required to complete the seal may be missing.
- Filters, regulators and lubricators (FRLs). Low first-cost improperly installed FRLs often leak.
- Open condensate traps. Improperly operating solenoids and dirty seals are often problem areas.
- Pipe joints. Missed welds are a common problem.
- Control and shut-off valves. Worn packing through the stem can cause leaks.
- Point of use devices. Old or poorly maintained equipment can have internal leaks.
- Flanges. Missed welds are a common problem.
- Cylinder rod packing. Worn packing materials can cause leaks.
- Thread sealants. Incorrect and/or improperly applied thread sealants cause leaks. Use the highest quality materials and apply them per instructions.
Leak Detection Methods
- Listen and feel – Only effective for large leaks in accessible areas where plant noise is minimum. Easiest and cheapest, such testing locates problem areas but does not provide useful information on the size of the leak.
- Soapy water – Effective for locating large or small leaks in noisy areas. It still requires access and does not provide data on the volume of air leaked.
- Ultrasonic Testing – Best method for large and small leaks (down to a pinhole). These portable devices can recognize the high frequency hissing sounds associated with air leaks. Ultrasonic testers have directional microphones, amplifiers and audio filters, with either visual indicators or earphones to detect leaks. Ultrasonic detectors use an electronic process called “heterodyning” which converts high frequency leak sounds into a lower range hissing that can be heard through a set of headphones. The operator manually moves the microphone to pinpoint the leak.
Fixing Leaks requires a Plan of Attack
Leak detection starts the process but fixing leaks requires an action plan. Life is far from perfection and so it goes with air leaks. A realistic goal should be to reduce leakage to less than 10% of total compressed air used. Start with the largest leaks; fixing the worst 20% of the leaks should reduce leakage by 80%. Large leaks and multiple repairs ideally would be conducted during a scheduled outage so as not to impact the production process, but small leaks should be repaired as they are located.
Rules of Thumb in Reducing and Preventing Compressed Air Leaks
- Check your connections – Most leaks occur at joints and connections. Many leaks can be fixed by simply tightening connections and checking fitting threads for worn or improperly installed thread sealant.
- Lower the air pressure demand of the system – By evaluating the system pressure requirements and lowering the pressure to the minimum range required for operation, the pressure differential across leaks is also lowered. In turn, this lowers the compressed air flow and hence the amount of air lost by a given leak.
- Review compressed air systems regularly, tag any elements that are wasting air, and take action to fix any large problems as quickly as possible.
For more information, please see:
[https://cbeuptime.com/how-to-detect-compressed-air-leaks/]
Maintaining Your Compressed Air System
Leak detection and repair is an ongoing process. A leak detection audit should be part of the maintenance plan at least every 12 months, especially as system components age or the system is expanded or repurposed. Training for operators to detect and a procedure to report leaks to maintenance personnel is highly recommended.
Conclusion
A compressed air system with minimal leakage is more efficient and more effective but like any operating system, needs maintenance. Leak reduction will immediately reduce energy costs, improve process productivity and reduce the facility’s carbon footprint. A leak repair program will yield a fast return on investment through energy savings, reduced downtime and scrap product. Leak detection, when properly addressed, will improve your bottom line.
For more information, please see:
[https://www.airbestpractices.com/system-assessments/leaks/finding-and-fixing-leaks]