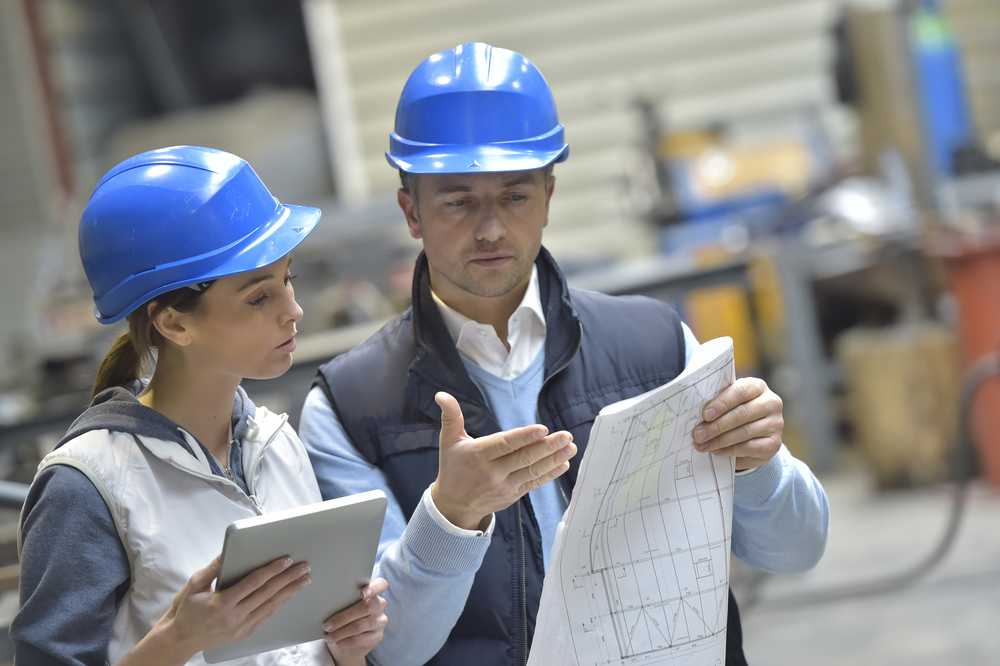
You can’t talk about reliable equipment operations without considering maintenance. But there are two distinct approaches to maintenance with drastically different outcomes.
On one hand, there is preventive maintenance that gets in front of problems. On the other, reactive maintenance addresses issues once their effects are evident.
Too often, plants have the maintenance mindset of ‘don’t touch it until it’s broken.’ While the approach may seem to cut costs on paper, it creates more expenses in the long run.
Reactive Maintenance = Increased Downtime
When everything seems to be running smoothly in a plant, it’s easy to put off equipment checks for days, weeks or even months. It’s not until you hear the sound of squealing bearings on motors and gearboxes, for instance, that you’re triggered to take action. And at that point, the matter becomes one of dealing with breakdowns during production time.
This is downtime when businesses can least afford it. Not only do facilities lose precious production capacity, but they also wind up paying staff overtime to finish up orders that were affected by the equipment downtime.
The other issue here is when failures do occur in equipment, plants with a reactive maintenance approach often don’t have replacement parts readily available. With the need to get equipment back up and running quickly, they can often find themselves at the mercy of suppliers and may have to wait days and weeks to receive critical parts.
Proactive Maintenance = Less Disruption, Less Downtime
Consider the scenario where instead of waiting for equipment to fail, you rely on time as an indicator for their replacement. Changing bearings, seals, and gaskets prior to failure, but with useful life left in the part is a good trade-off.
When plants take a preventive approach to maintenance, they tend to rarely, if ever have breakdowns during production. PM can be scheduled at hours most convenient to your facility’s operations, while saving the added time and costs tied to major repairs.
A robust preventive maintenance program also accounts for replacement part needs. For instance, if a facility changes out the screen in a centrifugal screener based on set time intervals (before its life expectancy is set to expire), they’ll have the forethought to determine the parts they need to order and when to order them without feeling rushed or paying extra.
Bringing a PM Mindset to Automated Equipment
Many plants are still new to the use of automated equipment in their facilities. And it’s important to think through what this shift from manual to automated means from a PM perspective.
When considering automated control systems, think in terms of the automated warning systems that are built into your car. In a car, warning lights and alarms indicate low tire pressure and when to change your oil or other major maintenance issues. Let an automated control system do the same thing to avoid unexpected (and costly) production down time.
Automated plant equipment has its own playbook; it’s crucial to read through equipment manuals and come up with a PM plan that reflects the degree and type of maintenance that’s required. Your PM plan needs to be a specific for the equipment and the application. If you’re running a very abrasive material through the system, for example, you’ll want to take care to change out parts more quickly as they’ll experience more wear and tear.
Equipment providers should provide recommendations on routine and preventative maintenance based on the unique application for each piece of equipment.
Once you have a good PM plan, stick to it — and watch your plant operations benefit.