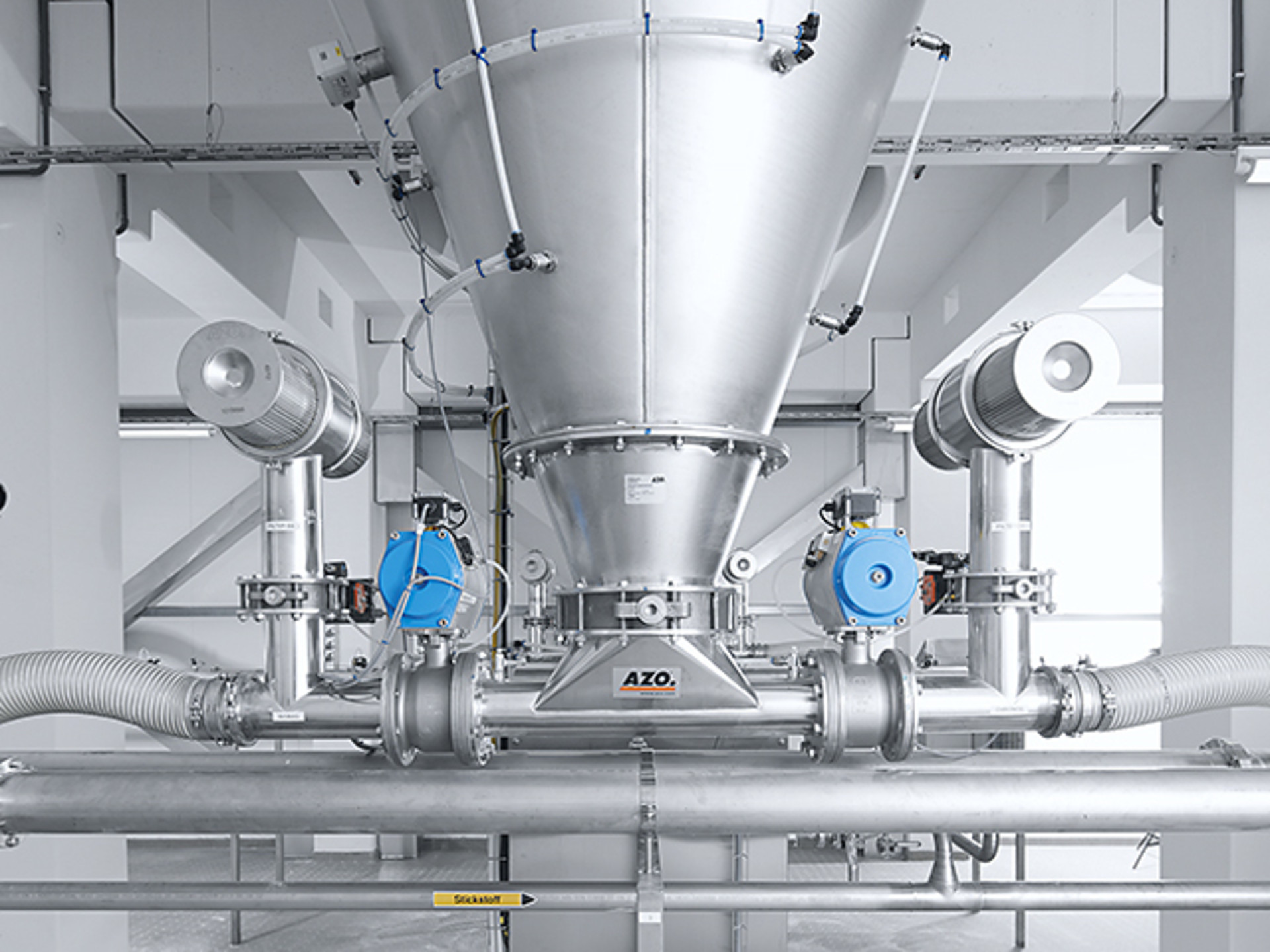
A pneumatic conveying bulk bag unloader system is a process by which dry bulk materials or powders are transported or carried utilizing a gas from a source to a destination. The bulk materials or granules are transferred through an enclosed conveying pipeline by the collective force of pressure and the gas used.. As critical as it may be to unload, reconfigure and convey material in any plant’s processes, conditioning your bulk material may be equally as imperative. In fact, proper conditioning will mitigate risks that are related to recall, rework and downtime.
So how do you determine the proper conditioning methods for your plant’s material? You have to look at how materials are going to be used and how they are going to move through a system to define this. Essentially, there are two distinct times you could condition your material: Pre-unload and post-unload. Most material conditioning occurs post-unload, but certain operations do occur before processes in which equipment like a bulk bag unloader is used (such as hydraulic crushing via proprietary technology).
Pneumatic Conveying System Best Practices for Conditioning Material
After unloading material either from a bulk bag discharge system or an intermediate storage vessel, there are other key methods of conditioning to consider. These include delumping, screening and using a magnet to detect ferrous metals. There are also a few indirect means of conditioning to describe, so we’ll go more in-depth on using a cyclone screener to condition your materials in another post.
These indirect means condition material using the application of dry air and controlling the temperature or humidity of the pneumatic conveying system. For certain materials, conditioning is generally accomplished before you perform operations like dosing and weighing material to achieve a precise batch.
Illustration of automated processes including AZO screeners before and after silos (TW and E respectively)
Let’s take a look at some common methods for conditioning by observing equipment used in processes and describing how to condition material indirectly:
Breaking Up Lumps and Clumps in Bulk Material With A Pneumatic Conveying Bulk Bag Unloader System
One common dangerous solution to breaking up lumps or clumps in a bulk bag is for an operator to attack the bag with a hammer, bat or mallet. Not only is this an impossible way to effectively break apart the material, but this also presents many safety concerns to the operator and even other workers. Using a hydraulic crusher to apply a few thousand pounds of force is both safer and more effective. These crushers are primarily used for poor flowing materials. There are different types of crushers, including big bag crushers (for conditioning bulk bags) and drum crushers (used with drum tipping or drum handling).
Another possible solution for some applications where material received in craft paper bags is extremely hard-packed into lumps is to incorporate a crown sieve vibratory grate into a bag tip station. A crown sieve is a perforated grate equipped with spikes. As the material is introduced to the bag tip station, the vibrating motor along with the crown sieve spikes break up hard-packed lumps until they are able to pass through the grate at the desired particle size.
An AZO Lump Breaker type KB 500 R (in round design)
Pneumatic Conveying Systems’ Lump Breakers, Magnets, and Metal Detectors
For material such as hard salt bricks that would tear a screen chamber in a screener, it is critical to use a lump breaker prior to screening. Lump breakers are active machines that use a common shaft with rotating hammers that break up chunks of material fed over the inlet, pushing the material through a gate and on to the next process. AZO offers lump breakers in two different sizes, as well as square or round configurations. In addition, we can outfit the device with extraction rails for easy cleaning and inspection.
Illustration of an AZO Lump Breaker type KBW 500 Q (cubic design with a roll crusher tool)
Magnets don’t change the characteristics of the material but take potential hazards (such as ferrous metals) out of the material. There are essentially two types of magnets: passive and active. Active magnets move inside of a chamber taking ferrous metals out of the material. When integrating magnets, it is important to first contact your pneumatic conveying system provider for proper installation so as not to negatively impact system performance.
Metal detectors find metals that are ferrous and nonferrous alike. They then divert such metal into waste upon detection. Some detectors accomplish this task with HRF (high-resolution frequency) technology, while others use X-ray technology for materials such as aluminum and plastic. Metal detectors are most often used at the end of a process before filling or packaging and make the material safe for public consumption.
Note: Proper conditioning doesn’t fraction materials, rather it takes the material in its natural form and alters it into a flow-able state. This is accomplished without changing the overall character of the material, whether granular or powder.
Pneumatic Conveying Systems and Temperature Concerns
As equipment like cyclone screeners represent a direct way to condition material, there are also indirect methods for conditioning bulk material by essentially conditioning their atmosphere and surroundings within a pneumatic conveying system. By controlling the temperature and humidity inside the convey line and introducing dry air to the system, you prevent moisture from allowing product to stick to filters, walls, pipes and receivers.
When humidity is a particular concern (like with many processes in the baking industry), you can condition the environment this way to make it more suitable for longer-term storage or a suitable condition for pneumatic conveying systems. A dehumidifier can be introduced if the product begins to build up in the pneumatic conveying system. This will help bring the relative humidity inside the system to an acceptable level where the material isn’t absorbing moisture out of the air. Oftentimes a dehumidifier can be added to an existing system if problems arise.
Other times the combination of robust equipment such as a lump breaker and a big bag crusher will do the trick. Let’s say you are conveying pharmaceutical-grade salts that are used in intravenous solutions: This material does not contain a flow aid to make the salts easily handled. When it is transported through humid surroundings and bought in bulk bags, at times, it will arrive as a single 2,000-pound block.
Specifically, AZO would use a big bag crusher to bring this material into the size of footballs. Then, a lump breaker will break these “footballs” back down to normal salt size to be conveyed. This example represents just one of many scenarios where you could condition your material effectively with common methods and specialized equipment.
Do you have a conditioning problem or an application you’d like to see improved? Contact our sales team for any questions on how to help your plant and processes run smoothly. We also offer a wide range of bulk bag discharging products that could fit your needs. Discover the best fit for your operation with our configurator.