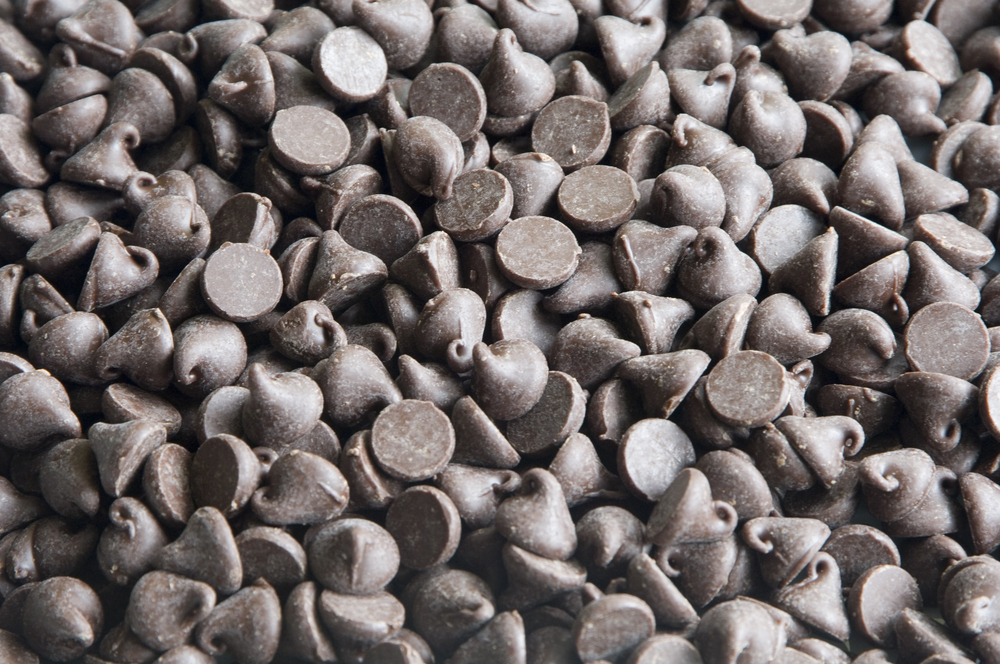
In the world of candy production, purity and safety are paramount, especially when dealing with bulk ingredients like sugar. Our story today centers around a candy bar manufacturer facing a very common challenge, how to upgrade a legacy manufacturing plant to meet current safety regulations. We'll delve into how AZO stepped in to address their needs and solve the problem.
The Company and Its Industry
A prominent candy bar manufacturer that specializes in crafting delectable chocolate treats loved by consumers far and wide. Production requires large volumes of bulk sugar, and their outdated material handling system is now considered a liability due to new government regulations concerning explosion protection.
The Challenge: Bringing Systems Up to Safety Standards
So this candy bar manufacturer was facing both safety and compliance problems. The Company had recently initiated a corporate-led capital plan to ensure that all their equipment, in all their manufacturing facilities, met the recently revised explosion protection standards set by the National Fire Protection Association (NFPA). Of particular concern was any location handling bulk sugar and the risk of combustible sugar dust.
AZO was approached by the plant engineers to address NFPA issues involving their legacy material handling system, roughly 20 to 25 years old, that lacked any explosion protection equipment. AZO has upgraded many similar systems in the past and to be successful, the new design had to be both technically and financially viable.
The Process Evaluation
AZO embarked on a comprehensive process evaluation, beginning with extensive discussions with the customer. The focus was on understanding the existing equipment, the potential explosion protection risks, the physical space required by the new equipment and the best way to retrofit the system to mitigate the known combustion risks.
Material Assessment Studies and Lab Work
Due to the complexity of the project, AZO opted to perform material assessment studies and lab work to augment the normal survey and design work. This was necessary due to the unique challenges posed by the combustible nature of sugar dust and the plant specific complications inherent in the existing plant layout.
Engineering Considerations and Innovative Solutions
As AZO delved deeper into the project, we made a pivotal discovery. An existing sugar vacuum receiver, in the legacy system, was discovered to be much larger than necessary. This is important because the size of the storage vessel is a primary variable in an explosion hazard calculation. An oversized vessel has excessive open space which increases the amount of suspended sugar dust, significantly increasing both the risk and power of any potential explosion.
This realization led AZO to propose a groundbreaking solution: replacing the existing vacuum receiver with a new, much smaller vessel that was right sized for the customer's current production needs. By doing so, the new design could reduce the footprint of the equipment and would require less explosion protection equipment. The candy manufacturer was thrilled with AZO’s innovative design and placed the order.
The Transformative Outcome
The implementation of AZO's solution brought about numerous benefits. The candy manufacturer now has a state-of-the-art system that is sized for their production needs and meets current NFPA regulations. This resulted in better system performance by reducing energy consumption and a more efficient conveying path from storage to production.
Additionally, the physical space required for the new system was substantially smaller, which improved space utilization within the plant. Most importantly, the reduced size of the equipment significantly lowered the risk associated with catastrophic sugar dust explosion hazards.
In conclusion, this partnership between AZO and the candy bar manufacturer underscores the importance of safety, efficiency, and innovation in AZO’s unique problem solving approach. Their journey together is a terrific showcase of AZO’s impact with expert engineering and thoughtful problem-solving to deliver both safety and operational excellence in the confection industry.