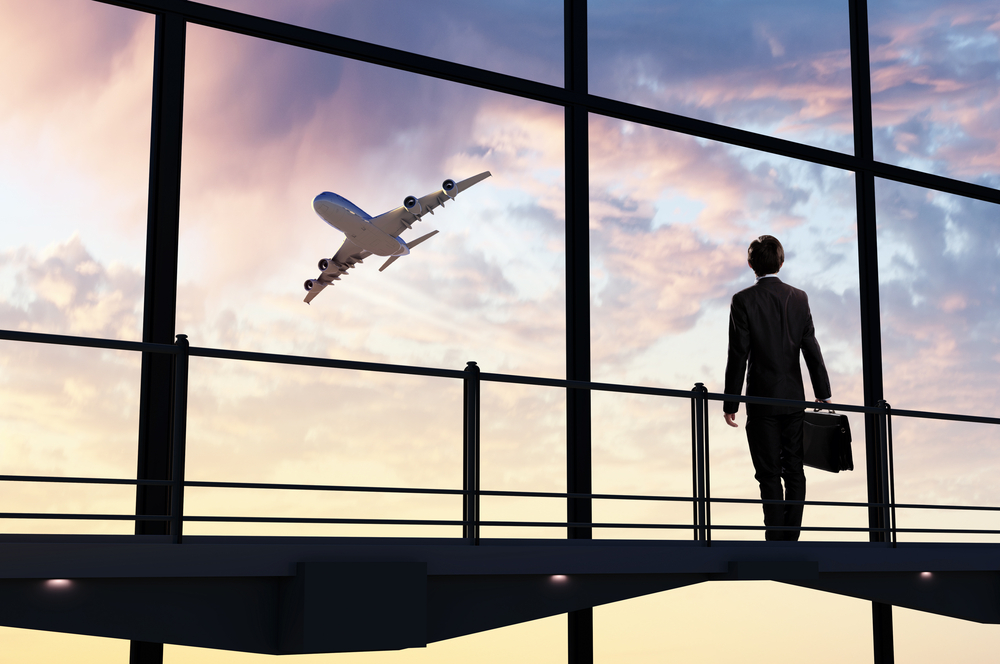
Year end Holiday travel is always a stressful time of year for airlines. With millions of Americans flying across the U.S. to see loved ones, airlines have more crowds and flight logistics to oversee than at nearly any other time of the year. It’s a chance for airlines to shine, or as was the recent case with Southwest, for organizational cracks to show.
While winter storms and staff illnesses contributed to flight cancellations across multiple airline carriers over the holiday week, Southwest had exponentially more cancellations. According to FlightAware, 90% of Southwest’s flights were canceled on Wednesday, December 28 — 2,500 flights in total. Meanwhile, Skywest had the next highest total of cancellations: 77.
The continued disruptions at Southwest days after the storm were due to Southwest’s outdated scheduling software. While enough staff was available and prepared to assist with scheduled flights when the weather cleared, the software was not equipped to keep up with the locations of staff or assign them in a timely manner. So, crew schedulers had to handle this step manually, which turned into a long and drawn out process — and well, the rest is history.
The Southwest story is a reminder of how legacy technology glitches can have a big impact on operations — a sentiment that we also understand here at AZO.
Time to Upgrade or Replace Your Control Systems?
With the above example of Southwest, it may be time to review your control system even if you’ve had no problems. If upgrading your software could prevent a disaster, like an extended production t system shutdown, wouldn’t it make sense to do it before it fails?
Upgrading control systems can be complicated. Ask yourself this first question: can it be upgraded or is an entirely new control system necessary? To answer this question, the manager should first investigate all the options available.
Let’s start with electrical components. Different scenarios call for upgrades or replacements of specific components. Simple replacements occur when a component wears out and a new, equivalent part is put in its place. For example, a failed PLC replaced with the same model number and firmware version would be considered a “replacement.” Upgrades involve replacing equipment/software with a newer version, which might provide added functionality (such as improving cyber security).
Software is a little trickier. And in the case of Southwest, an antiquated system is both complicated and expensive. Generally, software is identified by release numbers which inform managers if their control system is up-to-date. Upgrades usually raise the release number. Upgrades that involve a small numeric jump (release 7.0 to 10.0, for example) might be possible. Upgrades involving large numeric jumps (release 3.0 to 10.0, for example) could require multiple steps (from 3.0 to 7.0, then 10.0). In the worst case scenario, release changes may simply be impossible. If an upgrade is not possible, then a completely new control system may be required. Ultimately, you will need to talk to the manufacturer or software developer to know how best to upgrade your control system.
It’s completely natural for a control system owner to have hesitations about upgrading a well-running legacy control system. The adage “If it isn’t broke…” is an argument this author commonly hears. Still, the simple truth is that reliable production (and ultimately your bottom line) depends on the efficiency and reliability of the control system. In Southwest’s case, they are one of the best run, most profitable airlines around. But even great companies can run the risk of complacency, and after Christmas 2022, Southwest may have to reconsider some of its old ways. Their scheduling software the system was developed “in-house”, and there were no “newer versions” available. Replacement was going to be expensive and complicated so they didn’t do it. So while their “if it isn’t broke” philosophy worked for years, they weren’t prepared for a massive freeze up that exposed the vulnerability of their legacy software.
Other Common Misconceptions with Upgrading
There is often the fear that the new control system simply won’t work after the new upgrade is installed. This opinion is especially strong if the owners have had negative experiences in the past. While this concern is understandable, it is more about the integrator that botched the upgrade than the reliability of the new control system. As we saw with Southwest, postponing software upgrades can have their own massive costs if things break down at the wrong time.
To learn more about Automated Control Systems, and when to upgrade or replace them, view our comprehensive guide located here: https://www.azo-inc.com/intuitive-control-systems