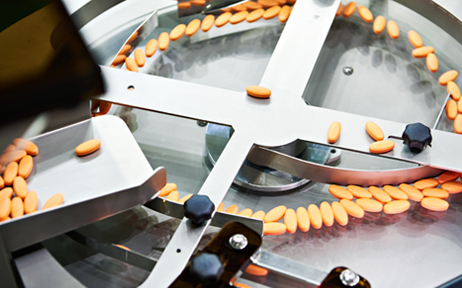
The U.S. pharmaceutical sector is at a turning point. After four decades of shifting API and dosage manufacturing offshore to countries like China, India, and Ireland, the pressure is mounting to rebuild a secure domestic supply chain. Today, just 12% of the active pharmaceutical ingredients used in U.S. medicines are actually made here.
It may seem as if the shift is due to recent tariffs, however, pharma has been making these plays quietly since the pandemic. COVID-19 exposed the vulnerabilities of global supply chains, pushing pharma manufacturers to rethink where and how their products are made. Plus, conditions in the 1990s that once favored offshoring factories are no longer relevant. Environmental laws are stricter and tax rates have changed.
Shifting tariffs and ongoing trade tensions have accelerated the timeline for these projects. In May 2025, federal policy reinforced the push to reshore pharmaceutical manufacturing. An Executive Order directed federal agencies to streamline approvals for domestic drug production, reduce permitting delays, and accelerate construction timelines for API and finished drug facilities.
The Food and Drug Administration (FDA) has been tasked with expediting plant approvals and tightening oversight of foreign manufacturers, while the Environmental Protection Agency (EPA) and Office of Management and Budget (OMB) are coordinating to remove regulatory bottlenecks.
Pharmaceutical Manufacturing’s Comeback in the U.S.
In 2025, major pharmaceutical firms made their plans known.
- Eli Lilly announced a $50 billion investment to build three U.S.-based API plants and one sterile injectable facility, creating over 3,000 skilled jobs and supporting a large-scale OSD weight-loss project in Puerto Rico.
- Roche announced a $50 billion plan focused on expanding U.S. manufacturing and R&D.
- Novartis also committed $23 billion over five years to upgrade its facilities in Florida, Texas, and California. They aim to produce 100% of their key medications for the U.S. market domestically, including APIs, biologics, and radiopharmaceuticals.
These moves reflect a growing push for supply chain resilience, national security, and long-term economic investment on U.S. soil.
But moving production back home isn’t as simple as flipping a switch.
The Realities of Reshoring Pharmaceuticals
Even with federal incentives and industry momentum, bringing pharmaceutical manufacturing back to the U.S. is a long-term, resource-intensive endeavor. Here are the top challenges facing pharmaceutical manufacturers:
Timeline & Capital
Developing modern API or biologics facilities typically spans five to 10 years and commands up to $2 billion in capital, according to PhRMA. The equipment alone — often with lead times stretching 18 months or more — adds to the delay. Expanding current facilities isn’t any easier.
Labor Shortages
A lack of skilled labor, particularly coming from STEM-related fields and trades such as welding, has slowed progress on builds. Immigration issues present challenges that are actively affecting the workforce and adding pressure to the need for automation.
Infrastructure Gaps
While states like California, North Carolina, New York, New Jersey, and Massachusetts remain core centers of pharmaceutical activity, Texas, as well as Midwestern states such as Ohio and Indiana are gaining traction. These regions need robust infrastructure like power, logistics, and digital systems to support large-scale pharmaceutical operations.
Regulatory Barriers
Regulatory oversight is vital to safety, and navigating FDA, OSHA, and EPA compliance significantly inflates costs. Pharma manufacturers need to adhere to Current Good Manufacturing Practice (cGMP) 21 CFR Parts 210 and 211 because these regulations outline the FDA’s “minimum requirements for the methods, facilities, and controls used in manufacturing, processing, and packing of a drug product.”
Technical Precision
Over-the-counter (OTC) and prescription medications require precise ingredient validation, dosing, and traceability all under strict hygiene standards. Systems need to be properly designed to meet the challenge.
How AZO Helps U.S. Facilities Hit the Ground Running
As a critical partner for pharma manufacturers, we’re ready to reshore and invest in your U.S. production. Large A&E firms and EPCs are taking on these jobs, and companies like ours handle everything about the ingredient automation design. We meet challenges like:
1. Precision Ingredient Handling
Pharmaceutical powders like calcium carbonate, TiO₂, and finished blends require exact dosing to ensure every tablet or capsule meets therapeutic specs. AZO’s automated weighing and dosing solutions (e.g., COMPONENTER, Dositainer, ManDos) are engineered for micro-to-bulk accuracy and compliance.
2. Hygiene-First System Design
Contamination isn’t an option in GMP-compliant facilities. AZO equipment features ultra-polished interiors that resist dust accumulation and support fast, thorough cleanouts, ideal for allergen control and product changeovers.
3. Fugitive Dust Mitigation
Handling dry pharmaceutical ingredients often creates fine, combustible dust. AZO systems incorporate explosion protection and advanced dust collection to comply with NFPA 660 standards while maintaining plant safety.
4. Smart Automation for Safety, Compliance & ROI
AZO’s integrated systems include track-and-trace software, ensuring traceability across the supply chain for audit readiness and anti-counterfeiting. We also optimize ergonomic design for operator safety. This not only supports 21 CFR Part 11 compliance but also boosts efficiency and reduces labor dependency.
Reshore Smarter With AZO
Bringing pharmaceutical manufacturing back to the U.S. is a complex process, one that requires far more than tax incentives and capital. It demands a strategic shift in how production is designed, managed, and scaled.
AZO empowers pharmaceutical manufacturers to overcome core obstacles — precision, hygiene, traceability, and safety — to streamline domestic operations. For companies taking on the cost and complexity of reshoring, AZO’s engineered solutions make the investment worthwhile.
If you're exploring U.S. production or expanding your pharmaceutical facility, let's talk. AZO is ready to support your project with proven systems and pharma-grade performance.